So my lack of a plan almost caught up with me. I "conveniently" forgot that the frame of the 38T is 3/4" thick. There would be no way to just set a pair of "match" grips onto that thick of a frame. What was I thinking? Well, I was probably thinking that when I first saw the 38T I thought how nice and easy it would be to make some exact replacement grips. Which is true. This gun would be an excellent candidate for a nice pair of custom grips with minimal inletting--Unless you decide to make target grips--Then you have to make the frame fit INTO the grips. I think I've still got enough wood here to go forward. In retrospect, I should have inletted first, THEN gone to the scroll saw. At this point, I'm forced to fit the right side grip (because it has the least amount of material in the heel) first and that will dictate the left side's profile. I would have proceeded this way regardless, but I should have thought further ahead. I think my next move is to screw through the right side grip holes into the left and work some of the external dimensions as a whole unit. I've not yet figured out how to attach the left grip to the frame. The stock grip simply clips to the CO2 cartridge.
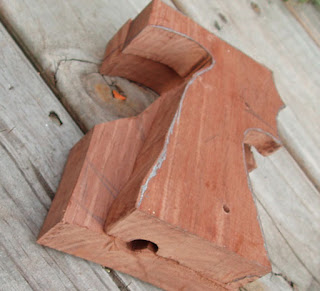
No, that's not dykem. It's just a silver magic marker. It shows up well under the sawdust as you're cutting.
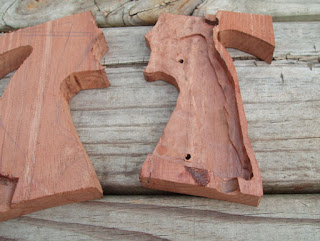
The inside won't be so pretty. I used a 30,000 rpm trim router for this.
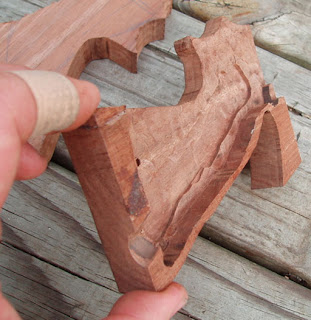
3/8" deep routing. Test fitting looks promising. I no longer wonder why Nill-Griffe gets $250 for a pair of these. You really need a milling machine to inlet something like this. http://www.nill-griffe.com/
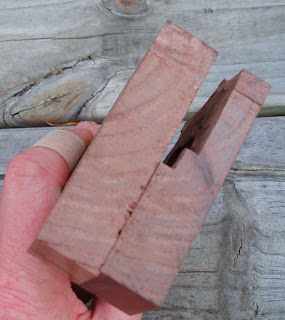
For the most part, the right will dictate the left. A palm shelf will come last. One bolt slot for the shelf or 2? More to ponder. And yes, I cut myself with a razor knife while scoring the walnut so the router didn't rip the corner off.
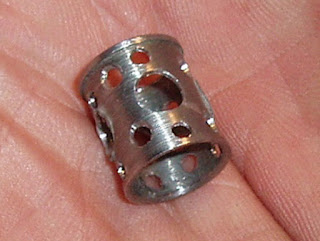
Here's my valve volume increase. Inside the valve, the sleeve serves to provide a base for the o-ring (140-058) and valve seal (38-094) to seat against. Just make this into lattice. Of special note: It's working. The pellet holes are substantially cleaner as they cut through the 10 meter targets. If I take it apart again, I'll try drilling a few more holes-- or it'll be slotted. I tried hanging a piece of tissue over the cylinder and looked for CO2 leakage at the transfer port as well as at the cylinder gap to the breech. Let's just say I've never seen a revolver so tightly fitted that it still functioned. On one hand I'm happy I was able to virtually eliminate any wasted CO2. On the other hand, it's getting harder to find any more power. I think I need to revisit that valve spring and see just how weak it'll go and still function.
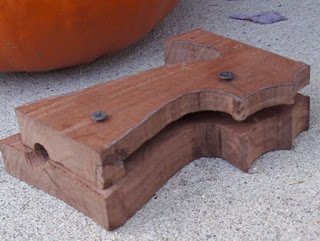
Now that the right grip has been inletted to fit the 38T's frame and the mounting screws have been located and drilled on the drill press, I've screwed the two halves together to shape the common sides.
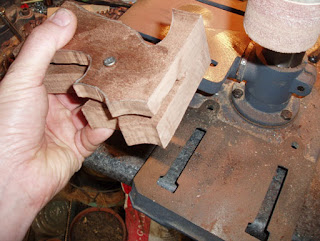
I chucked a 2" diameter sanding drum into the drill press and dropped the rpm. If you try to go too fast, you'll just burn the wood's surface. This let me sand the top, front and base as one piece. It'll fit tighter together this way and help eliminate unsightly gaps at wood to wood junctures. I used a charcoal mask while sanding. Black walnut can be an irritant to many people when inhaled.
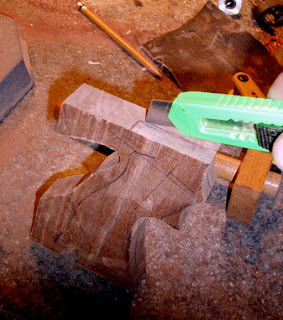
Time to inlet the left grip. I laid the gun's frame on top and traced. Scoring the line with a razor knife helps prevent the router from ripping out more wood than you intended to remove.
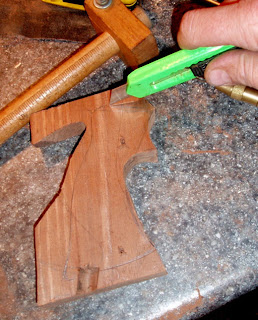
More scoring.
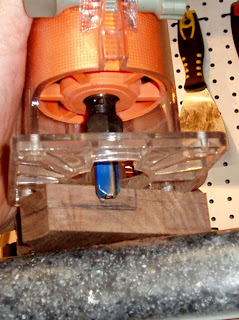
The trim router. Categorically the most dangerous shop tool I've ever used. 30,000 rpm helps keep the blade from tearing the wood. Whatever happens to the workpiece, do not under any circumstances let go of this tool. It will jack you up. It is extremely helpful from a control standpoint to get to full depth in several increasingly deeper passes. This tool is literally a wood eraser.
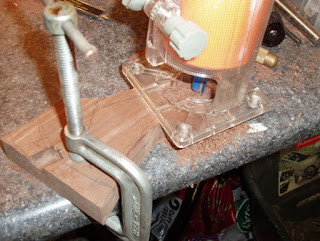
Anchor the work. Go slow and easy and you can write your name into the wood.
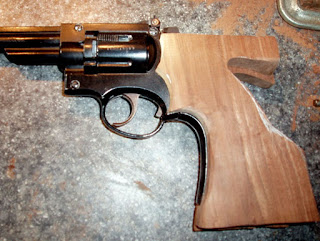
Test fit. The inletting is, to me, the worst part of the job. It's also, unfortunately, the important part because it defines how good the project will ultimately look. I am by no means good at this. I'm learning an awful lot as I go along. It helps that I have a few airguns with adjustable match grips to compare and pick the best features from. One of the challenges with a revolver is the bore height in relation to your grip. Getting your hand higher on the gun is better for recoil control as you get less torque from the muzzle blast. A non-issue here, but the lower sighting plane feels more natural. The "wing" at the top of the grip will be necessary once the adjustable palm shelf gets added later. The goal with a match grip is to envelope the hand and provide outstanding ergonomics for both sighting and control.
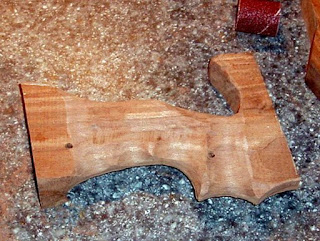
Back to the sanding drum. I used several smaller diameter drums to make the corners disappear and round the overall profile. Constant transfer to your gun hand ensures that it fits you. It's customary on the firing line to see match guns with wood putty, rasp marks and skateboard deck tape on the grips. Just making the tool fit.
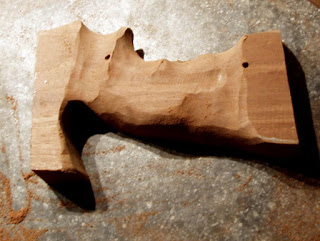
Roughed to shape.
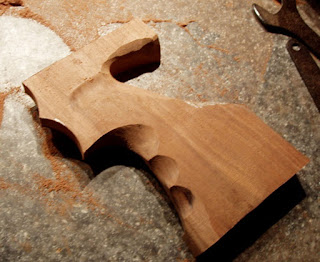
Left grip roughed to shape. Far less to do to this side.
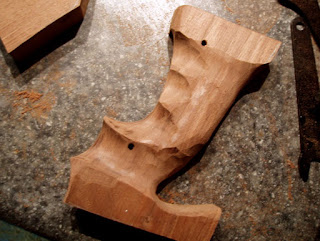
Slightly further along on the right grip. The finger notches are starting to show more definition.
1 comment:
Great stuff. Keep it up!
/Daniel
Post a Comment