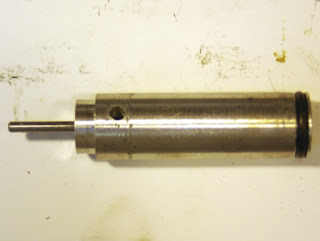
The valve assembly was pushed out of the tube.
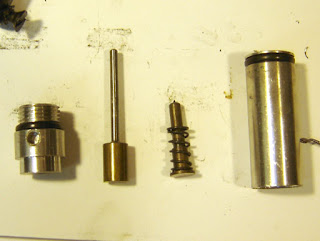
The valve assembly, disassembled.
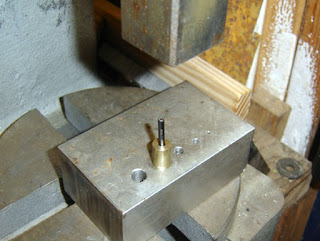
I used a short dowel pin to press the valve stem out.
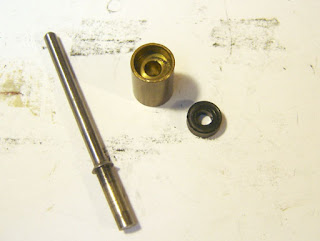
The disassembled valve.
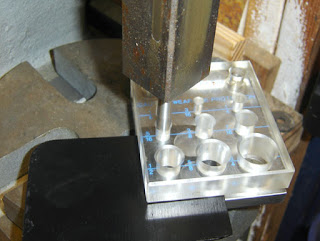
Using the directions in Airgun Hobby Vol. 2, Number 3, on page 43, in an article titled "How To Make and Install Your Own Valve Seals" by Peter Ruut, I stamped out a 5/16" diameter disc from 1/8" thick 95 durometer urethane rubber sheet.
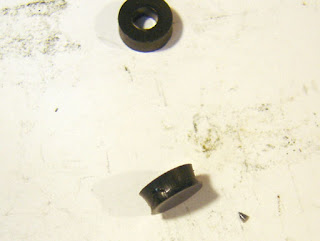
However I found that stamping the disc made the edge of the disc concave. This didn't seem ideal to me. I'm not sure why this happened, but will chalk it up to differences in material supply, ambient air temperature and possibly my use of an arbor press instead of a hammer...
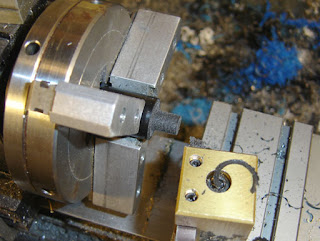
So I turned down some 95 durometer rod to 5/16" diameter.
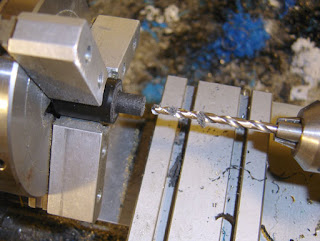
And drilled the hole for the stem.
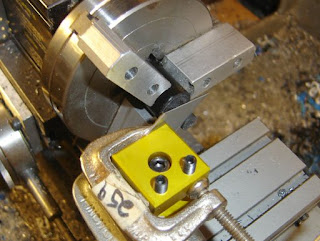
I clamped a utility knife blade to the toolpost and cut the face off.
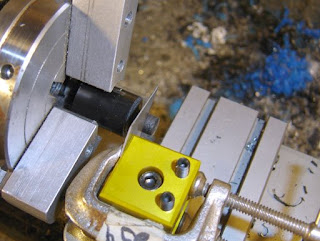
Then cut it to length. This worked well and gave a very smooth surface. I think I'll make a dedicated utility knife holder for the lathe.
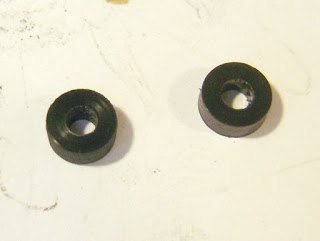
The new seal on the right, old on the left.
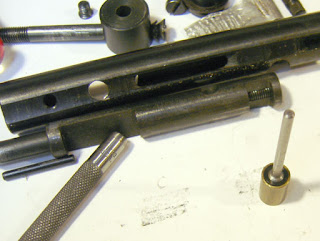
I pressed the valve back together. Notice the bolt in the picture with the cutouts for the cocking pins.
I assembled the rifle and it held gas! Two days later and it's still holding fine, so I'm calling this repair good. I did replace the other o-rings as well, which certainly didn't hurt.
8 comments:
Too much work. You could have purchased the seal for a few cents.
Working on the earlier non-cast trigger guard version of the 180, I noticed the valve stem on my gun only protrudes a little over 1/2 inch from the back of the valve body. It is much shorter than the one shown here. Is this correct for this gun or did someone chop it down for some reason?
The 180 and the 160/167 have different valves (and are quite different in many ways), so the protrusion is probably different?
Thanks Nick, yes I did look up the valve in my EVP doc for the 180 and it shows it with the shorter protrusion. Fortunately on the QB78 replacement valve I just received, the stem is longer so I plan to cut it down to match the length of the old 180 stem. Everything else appears to fit well. Before I do that, has anyone experimented with leaving the stem a bit longer to possibly push a little more charge time through the valve? It looks like the old one sits with just enough length to contact about 1/16" of the hammer center post through the spacer block. At some point would the spring pressure unseat the valve or is there far too much pressure from the gas to do that? Figured I'd ask first and cut second!
(Jack)
Hard to say but I bet if you ask on the Green Crosman forum you'll find someone who has done it before. I could see it refusing to seat if it was too long.
Nick
Where can I buy it... ?
Thanks
Where can I get it.. ?
Thanks
Where can I buy it...?
Thanks
Post a Comment