Derrick came up with a fun project last week:
We've both mentioned making a modification to the trigger blade on the Crosman 22XX series CO2 guns. There's not a thing wrong with the $9 trigger shoe from Crosman's custom shop. I've got 3 or 4 of those shoes. I wanted an easy project.
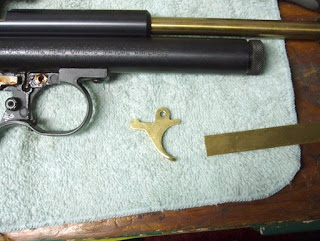
Here's a 2250 trigger blade. I think it's 5/32" thick. Without a trigger shoe to add width, it's painfully thin--to my finger at least--after 20 or so shots. The same trigger is used on the 13XX and 22XX guns as well as some of the older models. Since the trigger is solid brass, why not solder a piece of brass plate to the face of the blade and make an integral shoe?
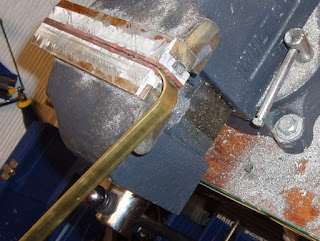
Found a piece of suitable 1/2" wide brass strip laying around. It's 3/32" thick. Cavalier as always about non-critical tolerance fits, I held one end in a vise and bent it around by hand.
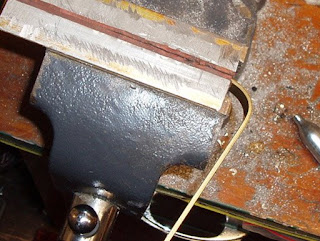
Initially, there was a glimmer of idea to wrap the brass strip around an appropriately sized cylinder. Turns out , that's a lot harder to do than it sounds. The brass, isn't that eager to bend to my will. Being a complete hack at heart, I just bent it as close as possible by hand in the vise.
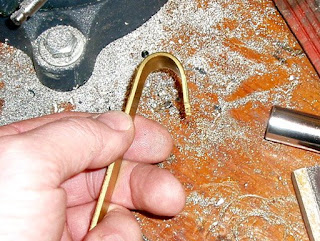
I ended up with this. The radii were promising.
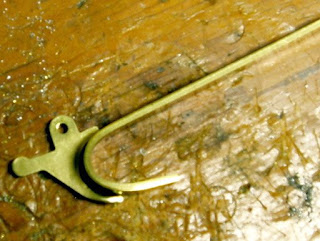
Close enough.
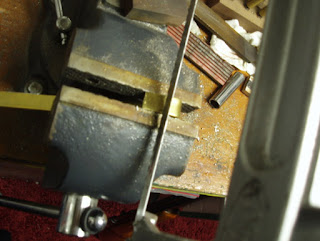
A couple quick magic marker lines and I hacksawed the ends leaving just the curve for the trigger. I decided at this point to do the bulk of the metal removal and final shaping after I'd soldered the parts together. Why? Easier to test fit my trigger finger to the unitized trigger parts.
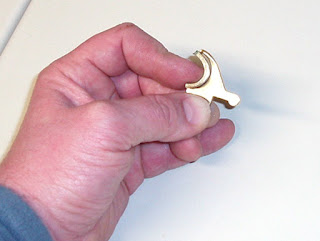
Another quick eyeball and back to the vise for a bit of filing and rough clean up.
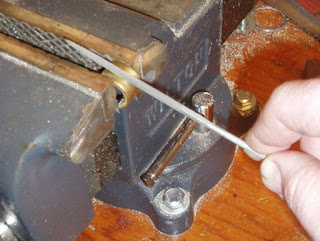
Crosman mashes the bottom of the stock trigger to make it very slightly wider at the base. It also interrupts the arc at the bottom. I filed a bit of metal from what will be the bottom of the trigger shoe.
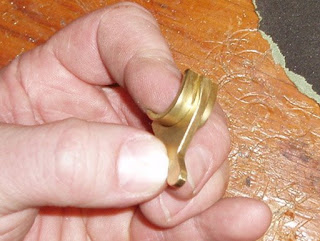
Another test fit.
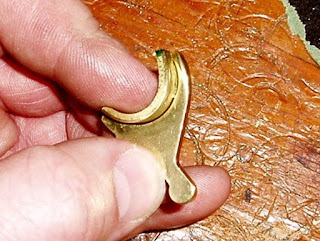
Who needs layout fluid when there's a big green Sharpie within reach? At this moment, I realized that I got lucky. Had I used a thicker piece of brass strip than 3/32", the trigger's face would now be too small for my finger. It would have been salvageable, but a substantial amount of time would have to be spent removing the excessively thick brass.
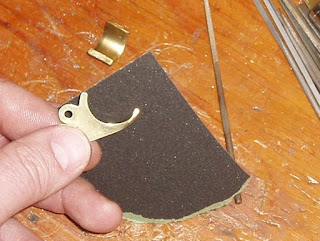
Sanded the surfaces to get clean metal for the solder. I chose to use 220 grit aluminum oxide paper because exhaustive, independent research has proven that it was on the top of my sandpaper box. If you're British, it's perfectly acceptable to use cabinet paper.
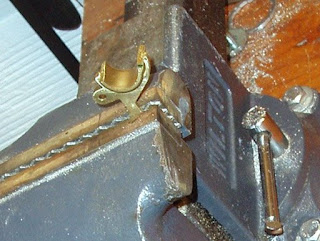
Here's my work holding jig. I know. Deluxe. You should see my budget for fixtures.
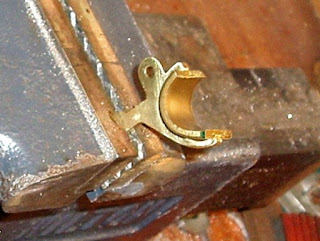
Gravity makes for a fine holding device.
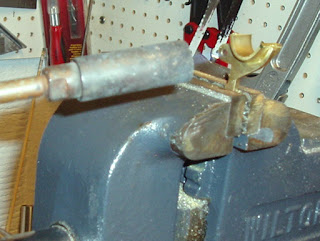
Fluxed with some appropriate plumbing-type stuff and out came the propane torch. If I make anymore of these, I'll get a cheap micro torch. There's benefit in heating small areas later to add and remove solder for cosmetic reasons.