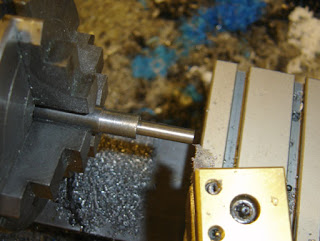
I turned an extra long shoulder that's 5/16" diameter, with a 3/16" shank, and parted off to length, leaving a short 5/16" diameter stub.
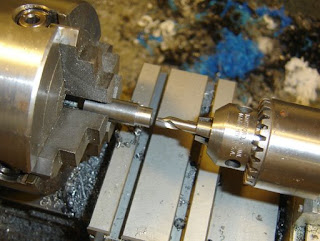
Which I then drilled.
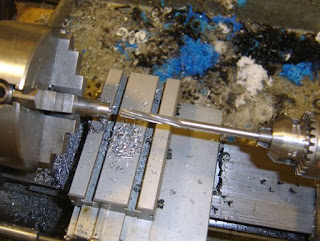
And reamed to 3/16"
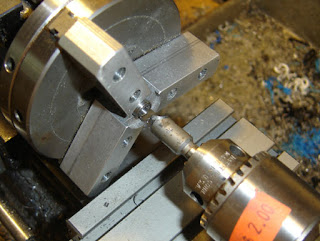
I then parted it off and deburred the cut off side.
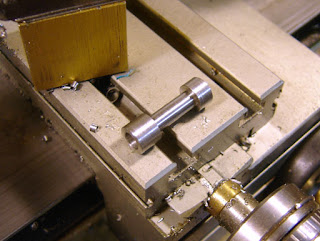
The new pin assembly.
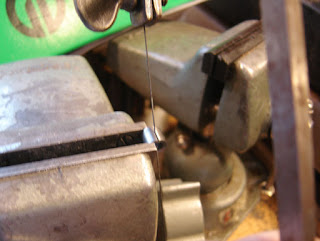
I used a jewelers saw to slit halfway through the bushing.
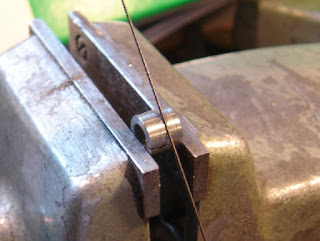
Then halfway the other way.
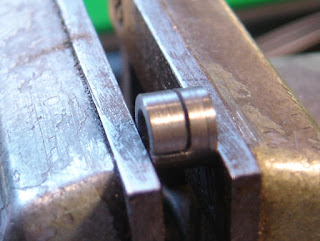
This leaves a section that can be compressed by the pin locking screw, which will retain the entire pivot pin assembly.
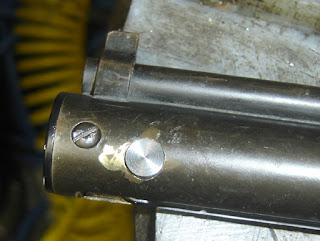
The head side of the pin in the counterbored hole.
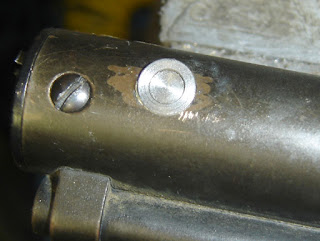
The bushing side.
The rifle pumps up fine now and I feel a bit more secure that the pump force is bearing on the tube rather than the tiny plug screws. The rifle seems a bit underpowered, as I'm only getting about 10 ft/lbs (580 fps w/14.3 gr. pellets) with 8 pumps, although another four pumps gives the same level of power. If I get bored in the future I'll tear the valve down and see if the seals need replacing, etc.
Another old ugly beater restored to functioning condition!