
The 38T was in pretty good shape cosmetically but with as most old CO2 guns (at least the ones I buy), when I inserted a CO2 cartridge gas spewed all over the place. Sigh. I downloaded the .pdf of the exploded drawing from Crosman. This drawing shows how all the components fit together and has instructions for rebuilding the valve.
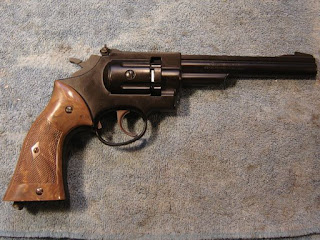
The is the other side. That screw in the middle of the fake cylinder holds the valve body in place.
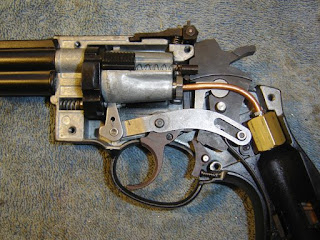
With the side plate removed you can see the mechanism and valve. Notice the small bushing that rides in the slot of the pawl arm. This can fall off if you flip the pistol over, so be careful.
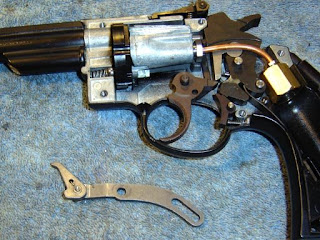
First up was to remove the pawl that rotates the cylinder each time the trigger is pulled.
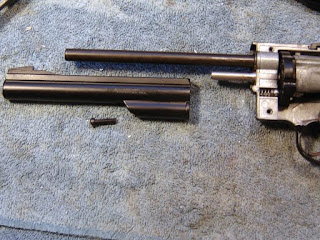
Then the barrel shroud retaining screw was removed with a long screwdriver.

The pin that retains the pellet cylinder was unscrewed.
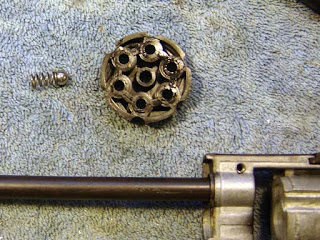
And the cylinder, spring and ball were taken out.

The screw on the back was removed and the valve assembly came free.
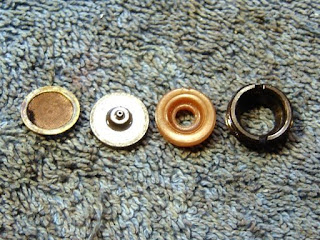
The CO2 cartridge seal parts were removed by unscrewing the black nut on the right. The seal itself seemed scarred up a bit.
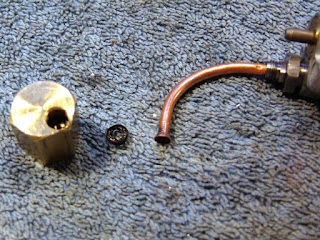
The copper line was pulled free after unscrewing the small gland nut, the seal seemed chewed up, whether by removal or age.

The other gland nut was unscrewed.

The valve requires a tool that clears the valve pin to unscrew.
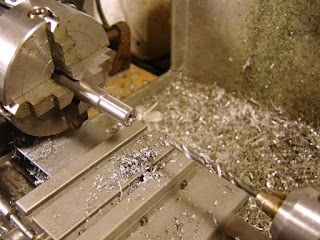
A piece of steel was chucked up, turned to a diameter smaller than the valve nut and drilled to clear the valve pin.
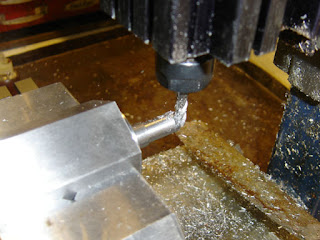
I then milled it to make a screwdriver type blade.

Not a complex tool, and you can just grind a small socket or screwdriver rather than machine a tool.
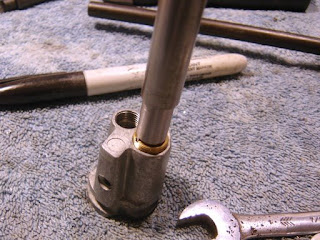
Unscrewing the valve nut.

The parts were removed.

The small black seal on the upper right is for the gas tube where it goes into the valve body. It looks bad but actually wasn't.
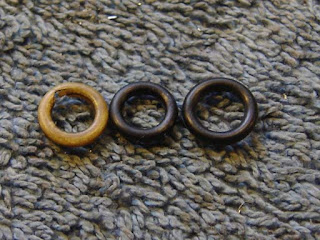
The valve o-ring on the left did have a big nick in it. So I replaced it with a buna o-ring. This is not ideal, and it would be better to use Viton or Urethane, but I figured it would hold long enough to see if the rest of the valve could be sealed.
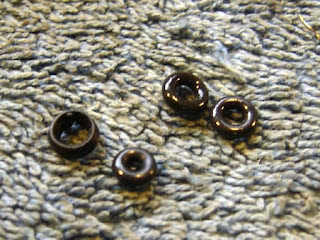
I replaced the small copper tube seal with a viton o-ring. Not ideal either, but I figured it would deform to seal. I was going to use the larger ones on the right, but the small one ended up expanding when placed on the tube to virtually the same OD as the original seal.
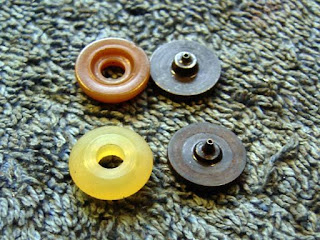
Luckily I had a replacement CO2 piercing pin and seal that came with another 38T I bought from the yellow classifieds. Otherwise I would have to hunt around for parts from the usual suppliers such as Bryan and Associates. Notice the difference between the parts - the new seal is a later design recommended in the .pdf from Crosman.
I was going to make a new seal out of Urethane rod or Teflon, but since I had the replacement part I figured I'd use it and see if the other repairs held. Now of course I'll have to find another leaky CO2 gun just so I can try making a CO2 seal...
Anyway, that's how you take one apart. To put it back together, just go in reverse...
I mostly made this post so I'd have pics should I take another one apart and forget what goes where.
A day later and the pistol has held CO2 overnight, shoots well, and I'm delighted. I now have 3 functioning 38T revolvers, 2 in .177 and one in .22.