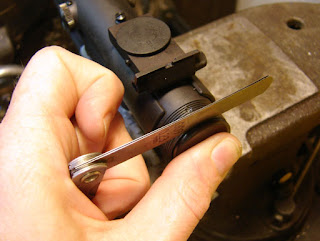
With the washer held against the rear piston seal I checked the gap with feeler gages. I showed .021" of gap. Going by my work on the Diana model 6, I want that gap to be .3mm, or .012". So I need to remove .009" off the face of the stepped washer. On the Diana model 6 I made a whole new stepped washer, which meant I could use the old Diana 6 washer for this purpose...
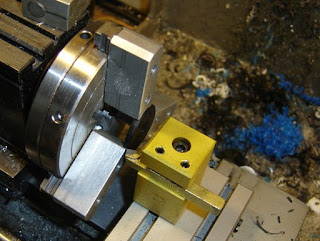
I chucked up the old washer and tried to face off .009...yikes! Totally hardened. Even with carbide I was having a very hard time removing material and getting a smooth face.
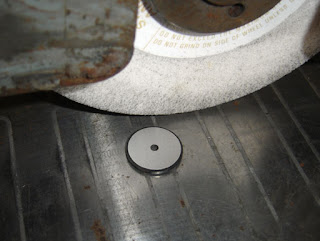
So I went out to my surface grinder and ground the face down.
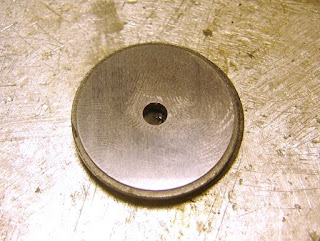
A lovely smooth finish.
I replaced the stepped washer, checked the gap (it was right on) and screwed the end cap back on.
I ran a bunch of pellets through the chronograph, the last 10 shots with RWS 7.0 gr. Meisterkugeln gave me between 491 and 503 fps. That's about what it should be doing.
How accurate is it? Much more accurate than I am...time to practice.