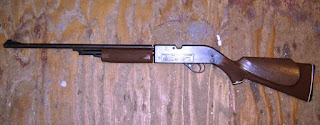
The Crosman 66
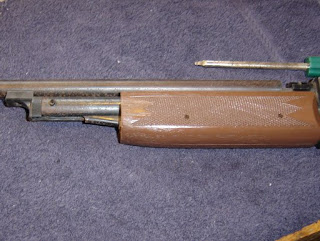
Notice the shroud is loose and rust freckled.
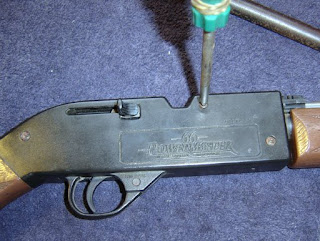
I used a square drive screwdriver to remove the three screws on the right side.
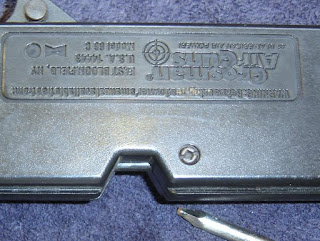
And one on the left.
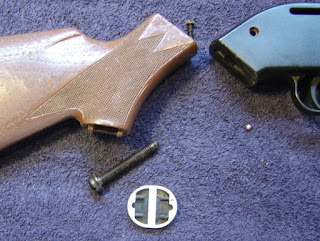
I popped the cap off the pistol grip and unscrewed the buttstock.
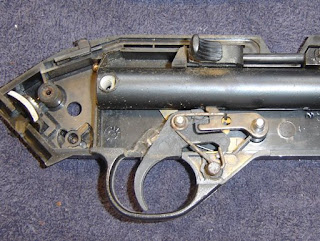
The trigger assembly. This picture is important for reassembly. You can't really make it out but there are cobwebs in the trigger assembly.
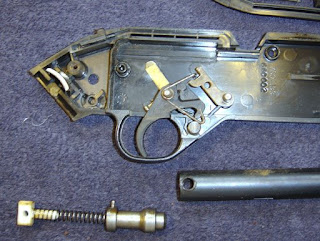
The hammer assembly comes out when the tube is pulled and the trigger parts go all the pieces...
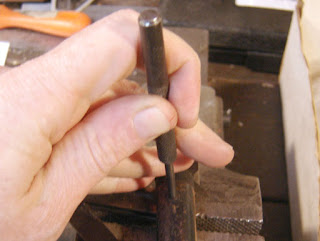
Punching out the pump pivot pin.
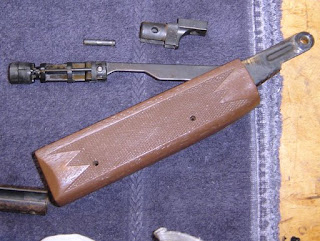
The pump arm removed. The pump seal was dirty.
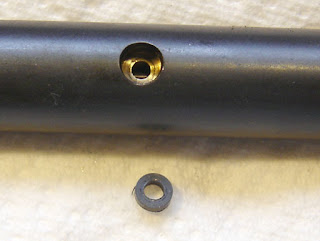
The small rubber seal for the transfer port was removed.
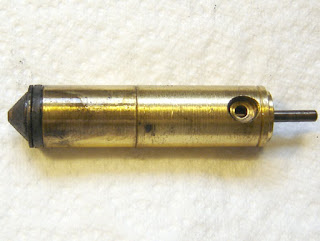
The valve assembly was pushed out the front of the tube. The pump end was really dirty.
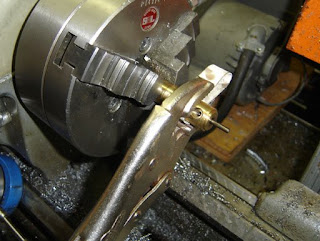
I chucked up one half in the lathe, locked the spindle and usncrewed the other half with a vise grip. The jaws were cushioned with a thick rubber band.
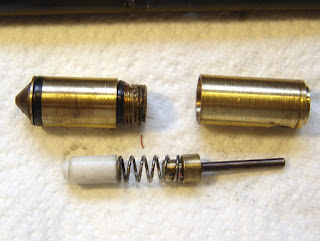
The valve, disassembled.
Everything in the gun is dirty. So I'll clean it all up and put it back together for the next post.