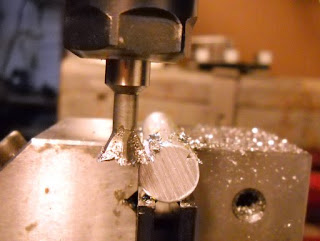
I drew up the dovetails in CAD but being paranoid decided to test the dimensions in aluminum rod.
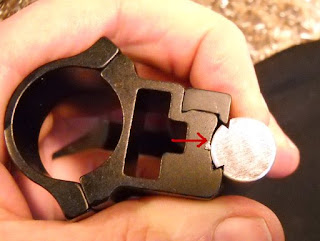
It's good I did as the dovetail was too deep for the mount. Notice the lack of clearance between the mount bottom and the receiver top. Every cheap cope mount is different, and there are no standards until you go with a Picatinny mount system.
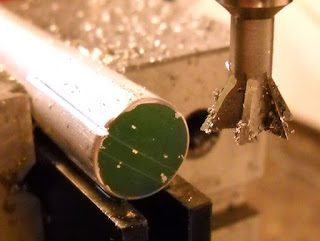
So I tried less depth of cut.
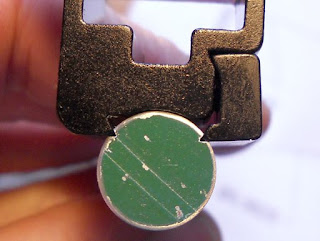
Too little.
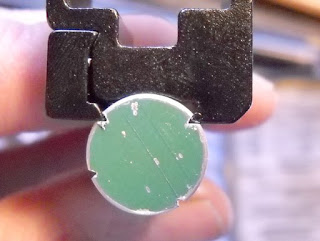
A tad more (ended up being about .050" groove width) and it looks good.
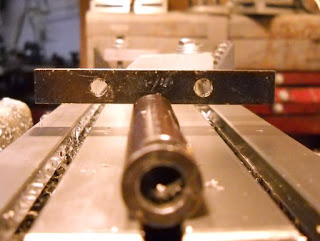
Then I had to figure out how to fixture the barrel/receiver on the mill. I decided to reference off of the loading cutout.
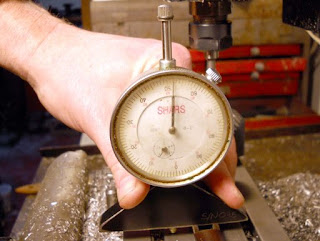
I finally hit on the method of using a dial depth gage to make sure the slot was horizontal. (a level would have been easier but nothing in my shop is level).
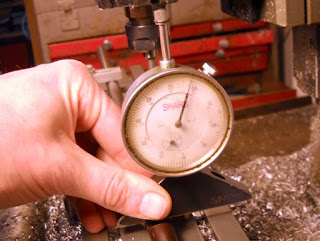
So I checked both sides, tweaked it, checked again until it was parallel to the mill table.
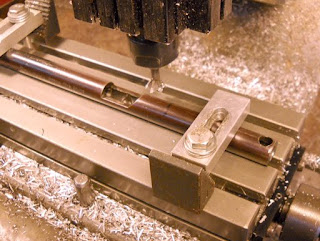
Starting the milling...
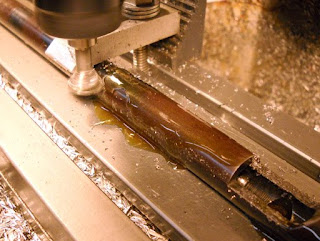
I used a lot of oil.
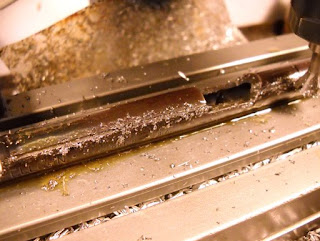
Worked like a charm!
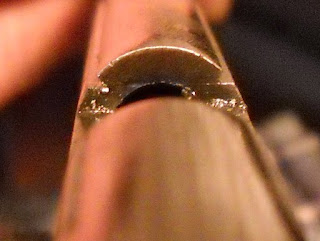
It was a fine balance between depth of cut, position, etc.
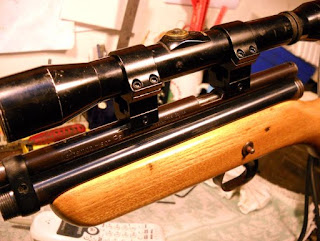
The scope mounted right up. My only quibble is I had to make the rear mount more forward than I'd like so it would clear the bolt handle.
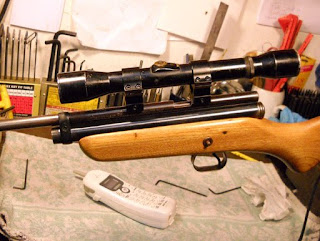
I think it looks good.
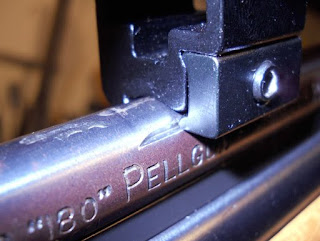
Just enough groove for the mounts to be solid and about .001" clearance between the mount and the receiver.