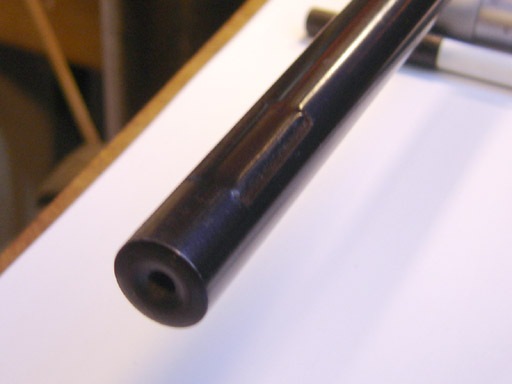
I didn't want to remove them on the off chance I ever get a set of the original, Original, sights. But left as is they are ugly and not entirely comfortable to grasp while cocking.
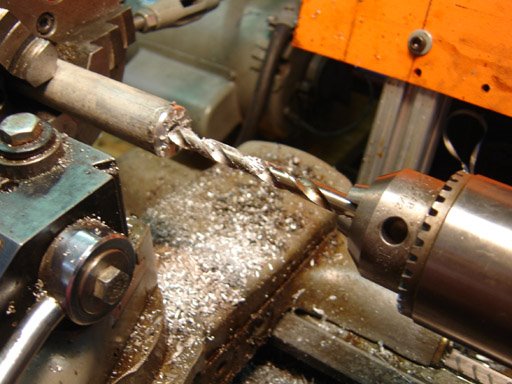
So I drill.
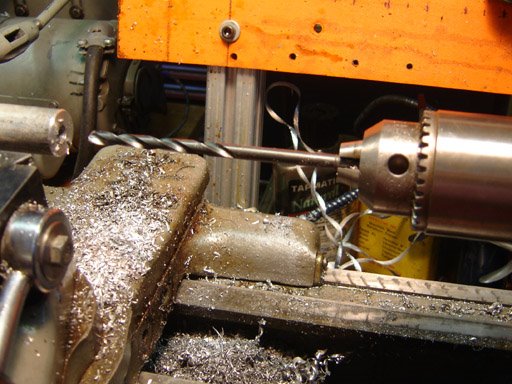
And then drill deeper.
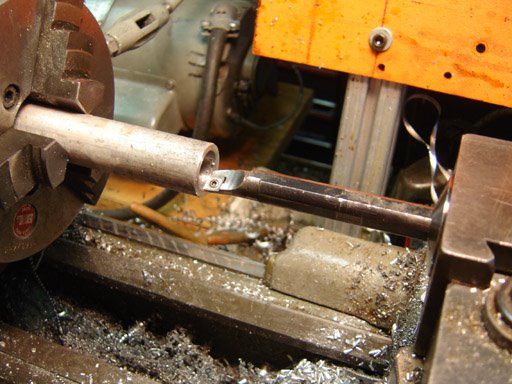
And bore to clear the grooves.
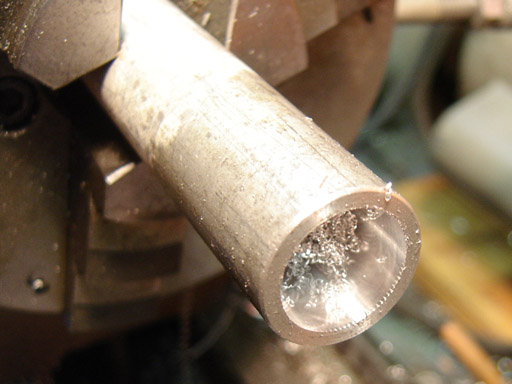
Boring picture of a bored tube.
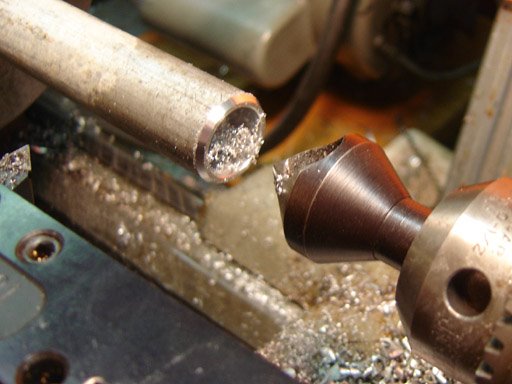
Deburring the hole with a large countersink.
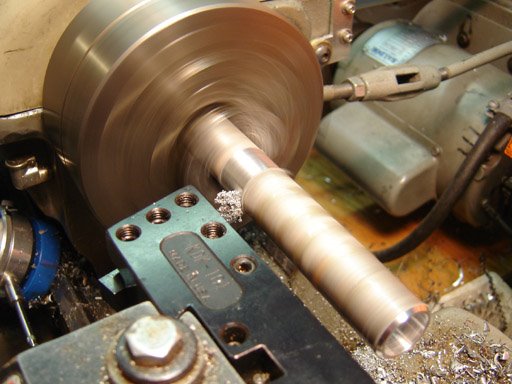
Turning down the OD.
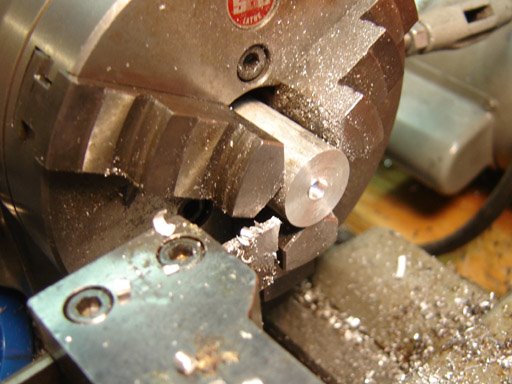
And parted off the rod.
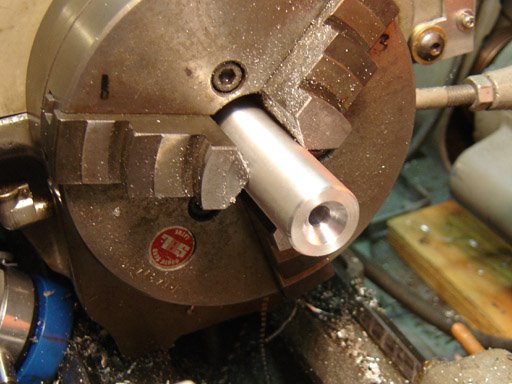
Flipped around it gets a rather large countersunk bore.
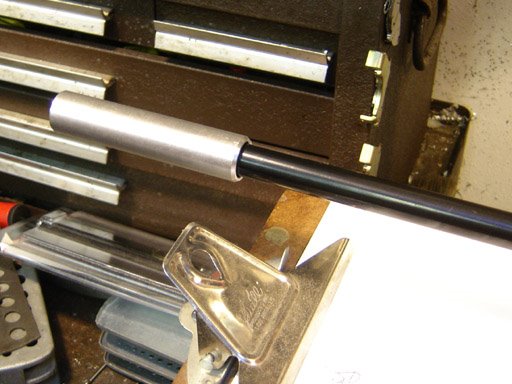
I thought I'd go for a minimalist tube look, but I didn't like it.
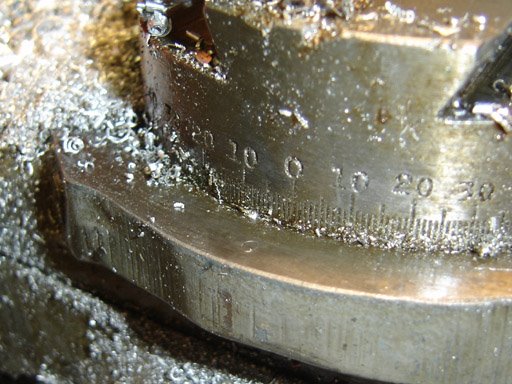
So I set the compound to about 3 degrees.
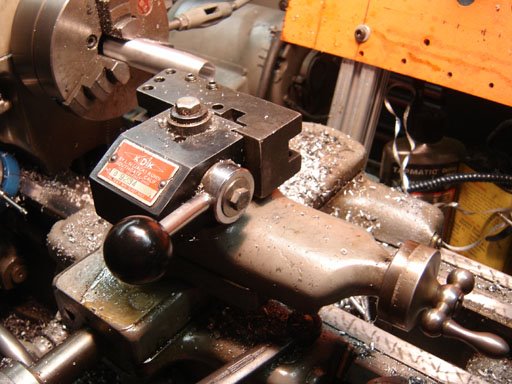
And turned a taper on it.
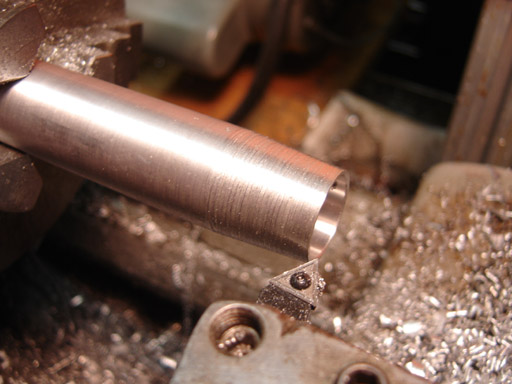
I took passes until the thinnest part of the tube was about .03"
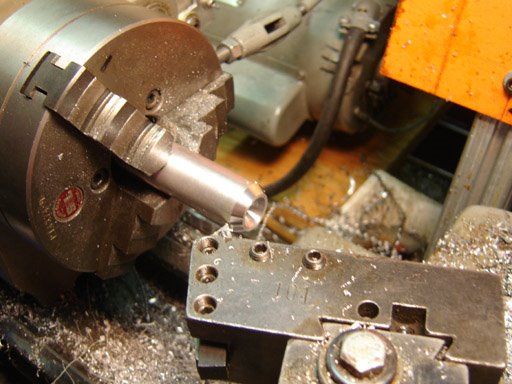
Flipped and tapered in the front to about 60 degrees.
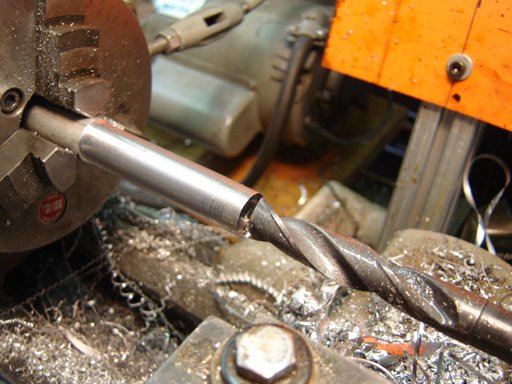
Making shims for the barrel.
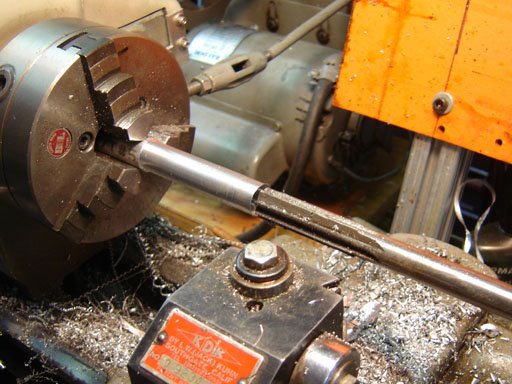
Reaming to the diameter of the barrel.
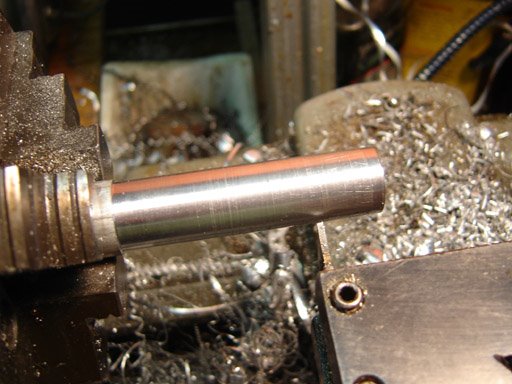
Parting off two bushings.
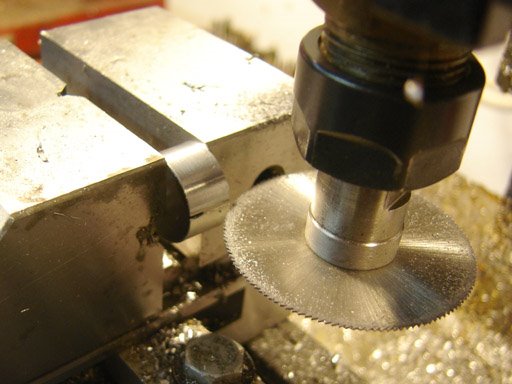
Slitting the bushings.
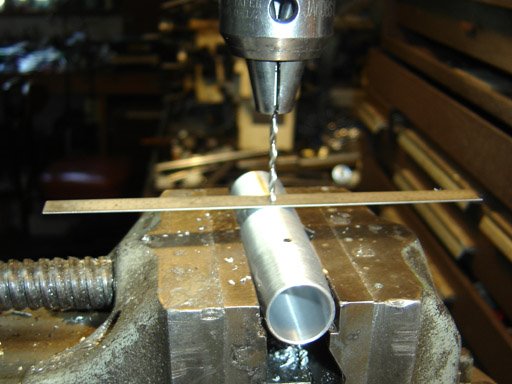
Drilling for two #4-40 tapped holes. Using a ruler in between the bit and a round workpiece will show whether the drill bit is centered.
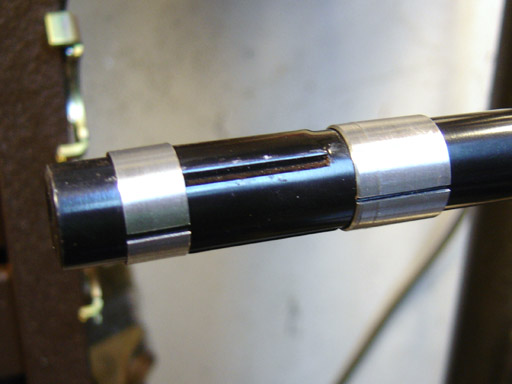
The shims on the barrel. These center the brake and protect the barrel from the setscrews.
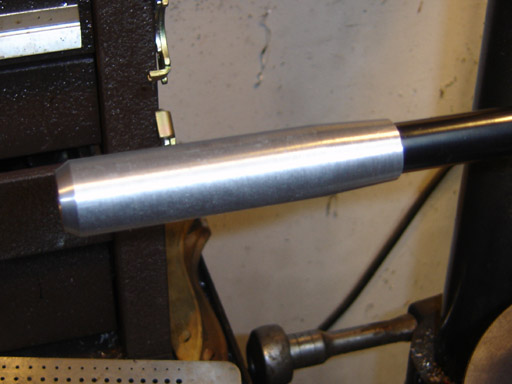
The finished brake (really a barrel protector and cocking handle). It's a bit big, but sort of has to be due to the front sight grooves. So while I don't like it on aesthetic grounds, I have to admit it is comfortable to use when cocking the rifle.
If I was really cool I'd send it out for anodizing, but instead I'm hitting it with some semi-gloss black paint. It seems durable on the Diana 6 pistol frame, and will be more easily touched up.