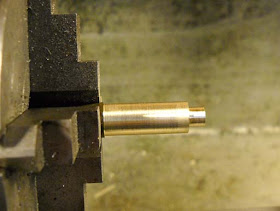
I turned up a plug for the muzzle.
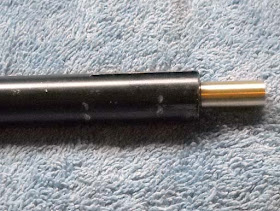
A slip fit.
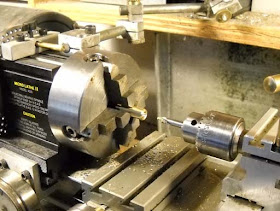
And added a center in the end.
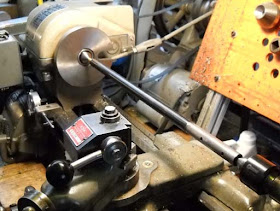
I mounted the barrel between centers on the lathe. The muzzle and breech end are in line.
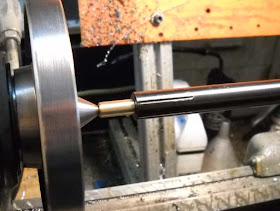
The plug...
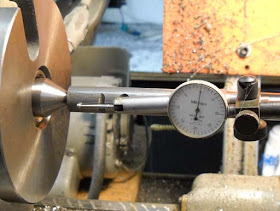
Running an indicator along the barrel shows that it's straight but...
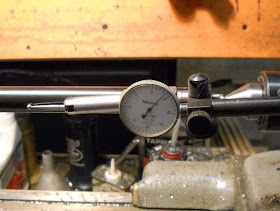
Not concentric. If it were bent then there would be a deviation in the middle of the barrel but the change in indicator reading was linear.(and I repeated this test all the way around) At least that's my analysis and I'm sticking to it.
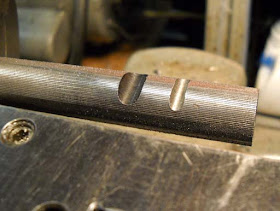
So I chucked up the barrel in the 4 jaw and turned down the breech end a bit so it would be a slip fit in the breech block.
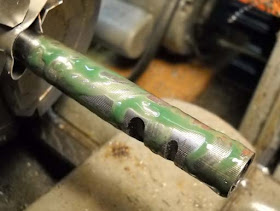
Slathered it up with Loctite 620
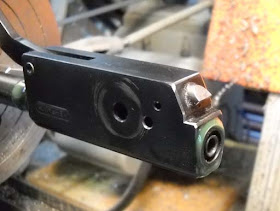
The excess squeezed out. I twisted the barrel around as I pushed it in to smear it evenly (I hope). I replaced the pin to keep it all aligned properly.
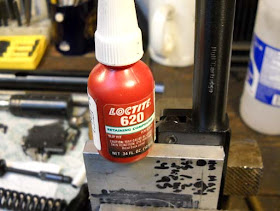
I left the barrel upright in hopes it would stay relatively concentric to the bore of the breech block and not sag. After only a few hours it felt rock solid.
Yes, still more to come...
Hello,
ReplyDeleteYou are one of the few blog that I check everyday to see if there is any new post. I love what you guys do and the way you do it. You need a TIG welder to do this kind of repair. A fairly cheap ($500) TIG inverter will work just fine for welding an new tab on the tube. Once you have one you will find a thousand use for it and with a very little practice you could make some very strong and nice welds.
This is the best blog ever.
Florent