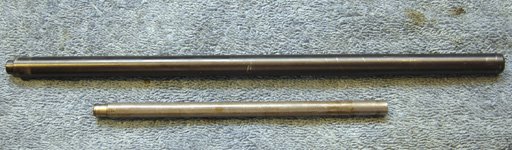
The 1377 barrel above the stock one.
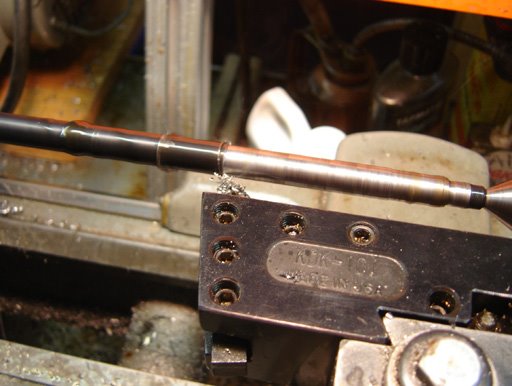
I gained a lot of respect for Crosman that day, as the steel they use for the 1377 barrels is some sort of profoundly hard and wear resistant alloy. Even with carbide tools I couldn't take a heavy cut.

So I just took pass after pass to get it down to the major OD of the 357 barrel.

It's a lathe, it's a gun, it's a lathe gun! That is, I tested for fit.
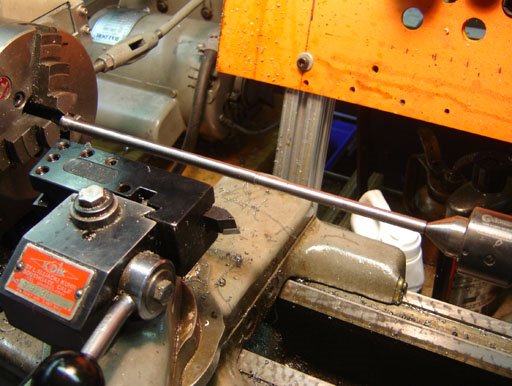
I turned down the minor diameter and filed it a bit. I got a terrible surface finish. I would probably have benefitted from using a follow rest, alas I don't have one. I cut off the bit left in the chuck as it had a perpendicular hole for the 1377 transfer port.
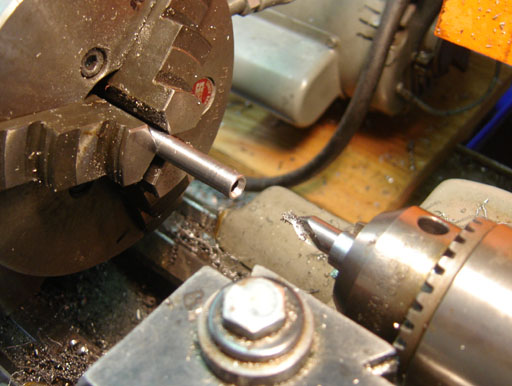
Using a 60 deg. center drill to make the lead in for the pellet.
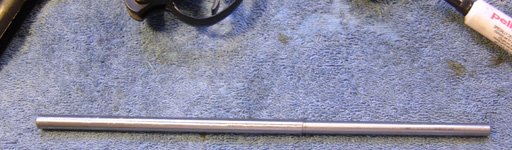
All done.
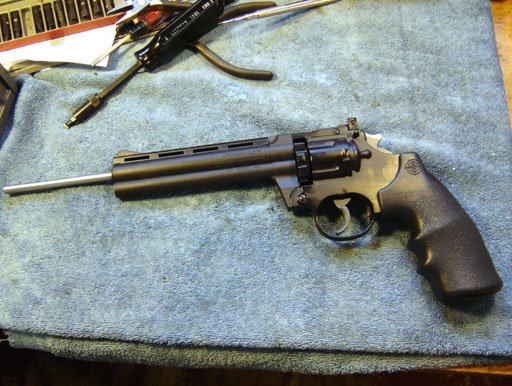
I installed the new barrel in the revolver and somehow it looked a little skimpy...

So I took a length of black acetal (Delrin) and drilled it to be a push fit on the barrel OD.
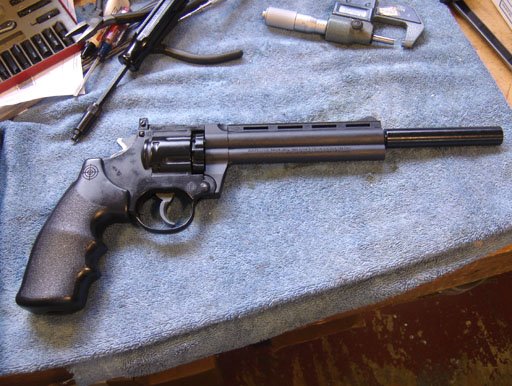
Is it cool, or lame? I don't know, what do you want for a $10.00 gun?
I chronied it using Crosman Premier Lights (7.9 gr.) and it got between 394 and 320 fps. over a course of 40 shots from a fresh CO2 cartridge, with the majority being in the 340-360 range. So did it improve the pistol at all? Probably not that much...
I much prefer the 38T's I own.
Complete BS Crosman barrels aren't some super wear resistant alloy. They are plain mild steel most likely 1018 or 1025. I have machined plenty before and so have others without any problem.
ReplyDeleteWell, I can only speak to my experience of machining the one, but it was much tougher than any of the steels I've machined in the past. Perhaps it was just that one barrel.
ReplyDeleteSo I did a test and found that another 1377 barrel machined terribly with the carbide tool. I then tried HSS and it machined well. So it doesn't like carbide.
ReplyDeleteI then tried a number of different steels with the same carbide tool, 316 stainless, hot rolled steel, 1018 cold rolled, and 12L14 ledloy. All machined beautifully with the same carbide tool that was having problems with the 1377 barrel.
I don't know why Carbide won't work for me with the 1377 barrel.
Nick,
ReplyDeleteDid you try using the carbide tool to cut the BS?
Derrick
ha wow that is cool. it may only be a 10$ pellet gun but i have a blast with them. you should try and oil the gun if its shooting kinda crappy. i bet its a whole hell of alot more fun with the huge barrel. are you worried about that pivot screw/hinge might brake?
ReplyDeletebut i give you a A++
As has been said, gun barrels and carbide tip tools are not well matched for machining. The problem probably is that unless the edge of the carbide tip is really keen and diamond lapped, then HSS tooling is the best for barrels.Using a travelling steady is recommended in slender jobs like these to eliminate springing in the mid section of the barrel.
ReplyDeleteI have used a round nosed HSS tool with good results on German gun barrels. High rpm and light cuts for the best results using sulphurised oil as a cutting lubricant.
Nick, I turned my barrel between centres because it was a multiple machining job.
David
Nick - I saw your article & got inspired . . .
ReplyDeleteHowever, I took the easy way out -
I have no lathe - So, rather than turn down a heavy barrel - I drilled out the ends & channel in the barrel housing by hand (literally) -
I removed the weight bar from the barrel housing - no need for that with a 'bull barrel' -
Begining with a reamer I opened up the ends of the barrel housing and then with the appropriate bit in hand drilled out the channel.
I snapped off the barrel tabs and filed down the nubs on the housing rib - I'll glue that down later.
I used a 10-1/2" piece of cut off from a 1760 barrel - Using the muzzle end for the feed side and I recrowned the cut-off end for the muzzel side. This allows the sight flat to be used to butt the new locking plate up to and the original crown (polished on a buffer with some jewler's rouge) is now the forcing cone.
I used a worn out 1377 lever link assembly, that happens to be .050 thick, to scavenge the metal to hand fab a new lock plate.
The .050 thickness of the new lock plate fills the lock plate slot in the barrel housing perfectly and keeps the barrel from drooping like the original stock set up does -
I secured the barrel & lock plate with set screws.
http://i263.photobucket.com/albums/ii129/WindyCitySquirrel/357W-/DSCN2972.jpg
http://i263.photobucket.com/albums/ii129/WindyCitySquirrel/357W-/DSCN2979.jpg http://i263.photobucket.com/albums/ii129/WindyCitySquirrel/357W-/DSCN2981.jpg
I haven't decided how to shroud the barrel yet - But it shoots a LOT better & quieter now.
RJ
RJ,
ReplyDeletePretty cool! Great work.