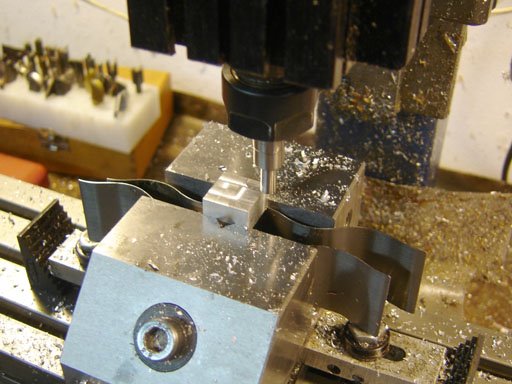
Finding the edge of a .625" x .625" x .375" block of aluminum.
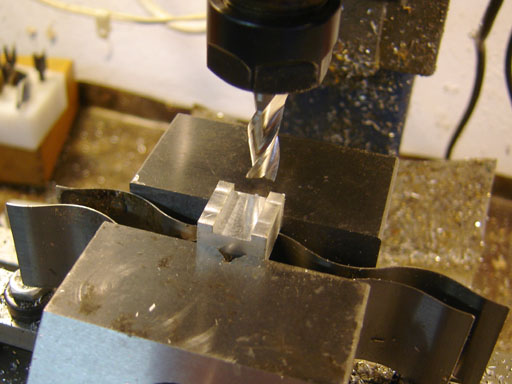
Milling the minor width of the dovetail slot.
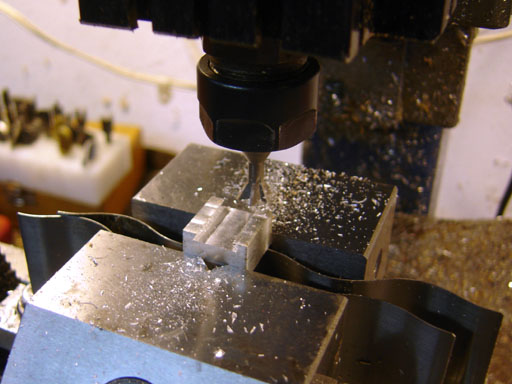
Milling the dovetail with a 60 degree dovetail cutter.
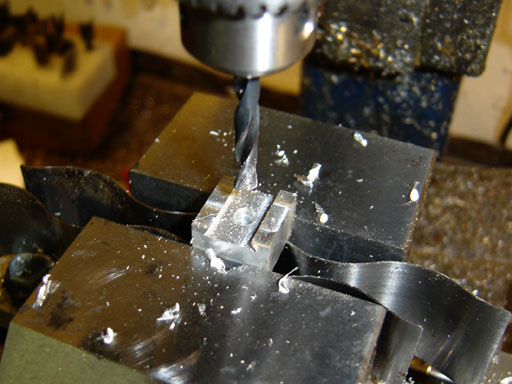
Drilling the hole for the stop pin.
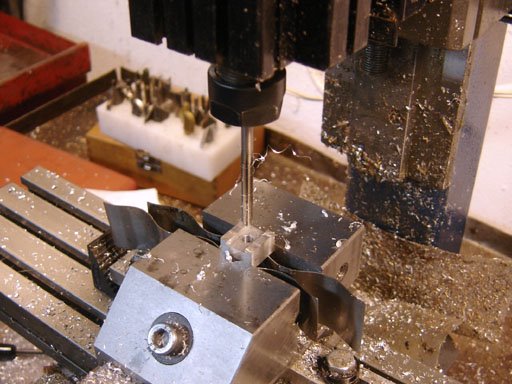
Reaming the hole for the stop pin. The reamer is held in a collet because of the lack of z-axis height on the Taig mill.
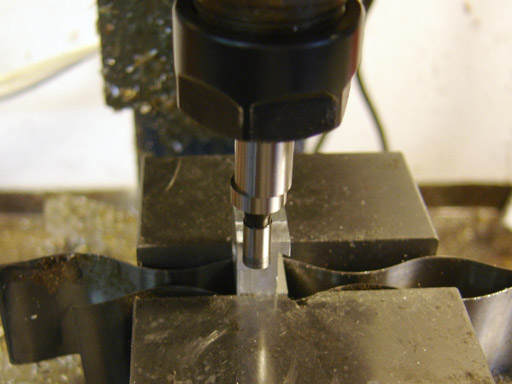
The work is flipped 90 degrees and the edges picked up again with an edge finder. Note the offset of the tip, this is what it looks like when it "kicks" out at the edge.
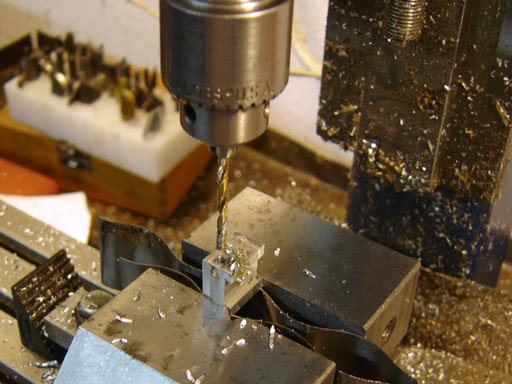
Drilling for the screw holes.
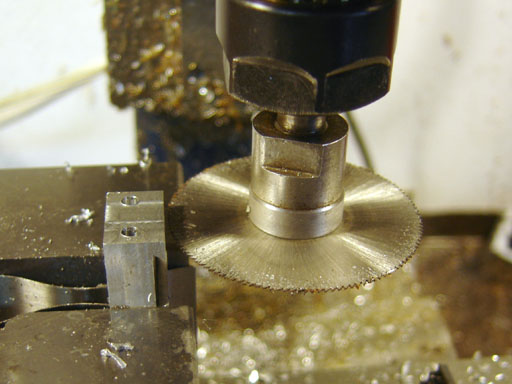
Sawing off one side of the dovetail. When I make another one I'll saw off both edges for better centering of the pin on the dovetail, but that's another story...
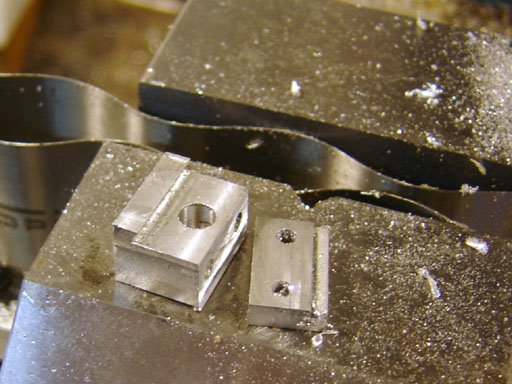
The two pieces.
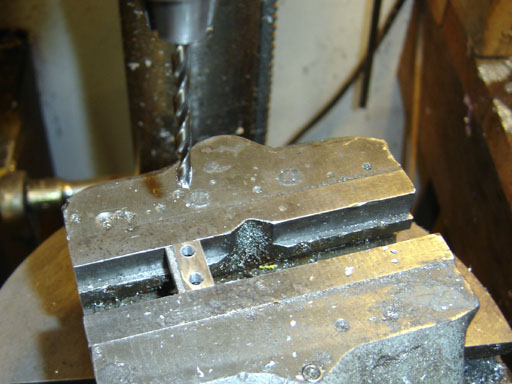
Drilling the clamp part for #6 screw clearance.
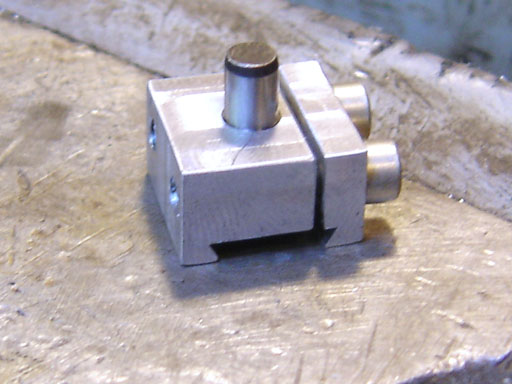
Almost finished...but not.
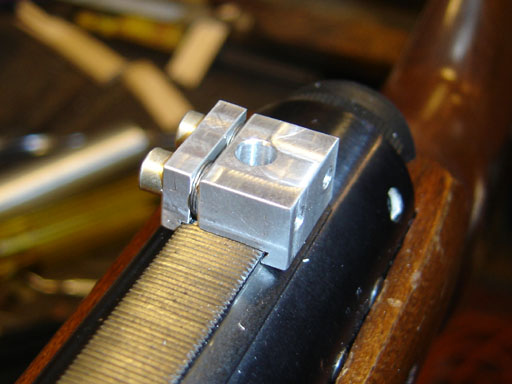
I found that adding several washers maintained uniform clamping.
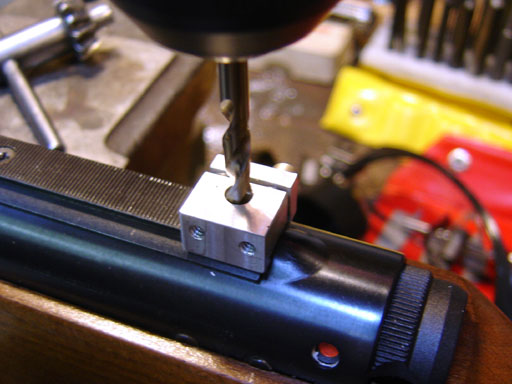
I then drilled a shallow hole in the scope rail, using the scope stop as a jig. I followed the drill up with an end mill to generate a flat bottom to the hole.

As you can see the hole is a little off center, as I said, it would have been better to make the stop adjustable for center.
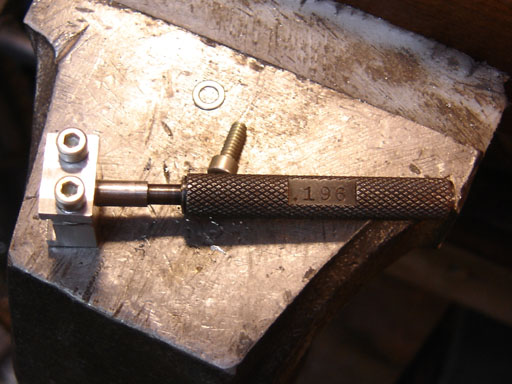
Drilling the hole unfortunately wallowed out the carefully reamed hole in the stop, so I couldn't use a dowel pin as I planned.
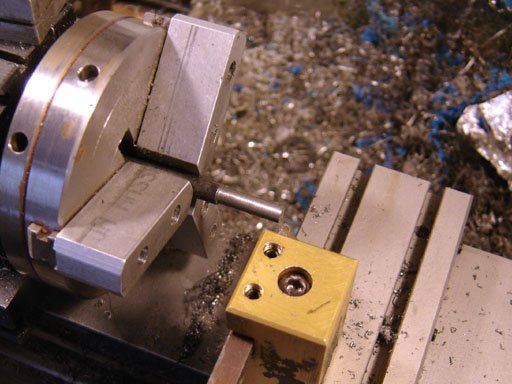
So I made a pin out of some steel.
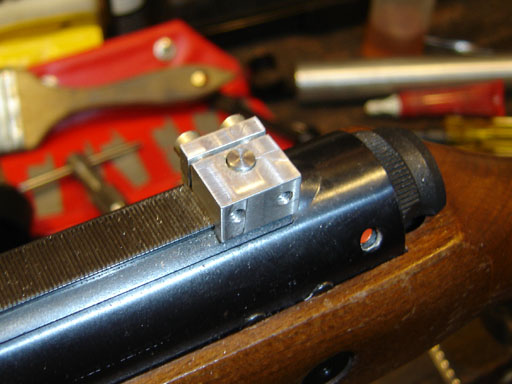
The completed stop. To prevent any movement, I used a small amount of loctite bearing retaining compound to lock the pin in.
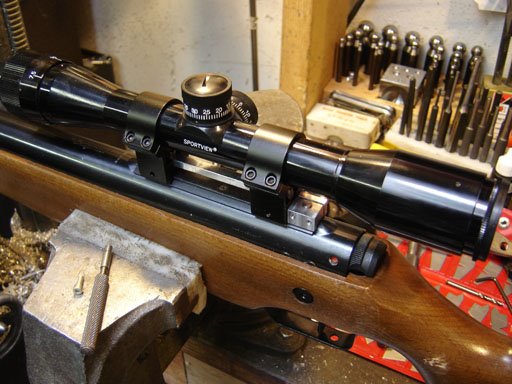
The scope mounted again...I made small witness marks so I could keep track of whether the stop moves at all. As with all my mistakes, er, experiments, I'll report any movement after I fire a few hundred pellets through. Today's post on the Pyramyd Air blog shows what can happen if movement does occur in a stop like this, but I think the addition of the loctite will prevent that.
Nick - what were your speeds & feeds when using the slitting saw?
ReplyDeleteThanks!
I ran it at 1300 rpm and feedrate, well I moved it slowly, say 2-5 ipm (I was cranking by hand). It is a fine cut saw, maybe 20-30 tpi,.016" thick, 1-3/4" diameter, I didn't have a coarser cut saw in that thickness so I had to feed slow or else the gullets would fill up with chips.
ReplyDeleteOh, I should add that I took several passes to get to full depth.
ReplyDeleteAh, ok - so just to clarify, rather than index the slitting saw directing into the part at 2-5 IPM, you took perpendicular passes of a smaller amount each time?
ReplyDeleteYes, I took several passes across. Plunging in isn't usually the best way to go.
ReplyDelete