Well Felice has a cold and stayed home today instead of going to work. So I went out with my youngest son Max to get some cold medicine. I had heard that Crosman airguns were on sale at the local discount store (Bi-Mart) where I was to buy the remedies, but only CO2 carts were on sale (20% off) so I didn't buy another 1377 pistol as I intended to. Once you get it into your head that the day is going the be an airgun acquisition day, it's hard to let go, so rather than returning directly home, we took a very long round trip and stopped in at the local non-pawn pawnshop. Anyway, I digress...At the pawn shop I bought a "Diana Pistol" and a Crosman Phantom (broken front sight) for $125.00 total, or $62.50 each, the Diana was priced at $89.99, the Phantom at $69.99.
EDIT: I found that my earlier recollection of the Diana at $69.99 was wrong, so I changed the price above to the $89.99 that was actually asked. This highlights the importance of always bargaining at pawn shops. I was able to buy the two guns for $35.00 less than the asking price.
The Phantom sight will get fixed/blogged later, I only bought it so I'd have a project, which is a bit perverse. I noticed a guy holding a bicycle pump as I was leaving, turned out to be a high pressure pump, as used on PCP airguns, but he saw it and bought it first, for $19 (you know, $200 less than it would cost new)! Oh well, you can't catch every fish in the sea.
The Details:
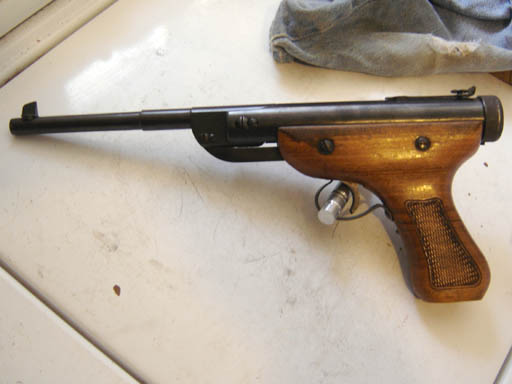
The Diana Modell 5. I say "V" in the title because that's what the Blue Book calls it. There is no "V" on the pistol though.
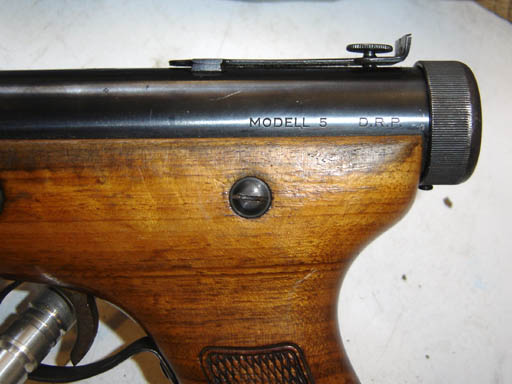
"Modell 5 D.R.P."
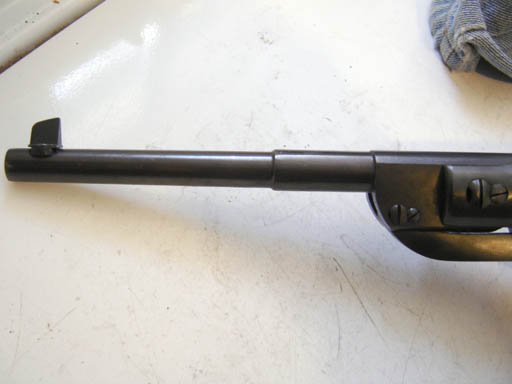
A nice stepped barrel
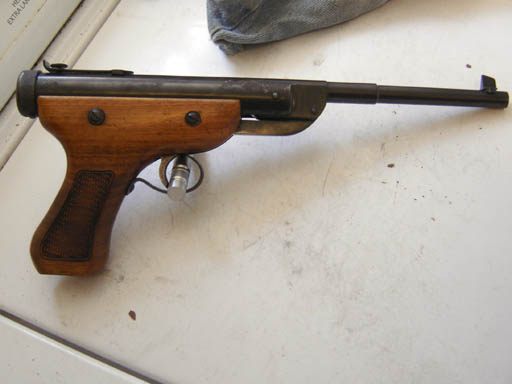
Two grip retaining screws with cup washers on each side hold the wood to the action.
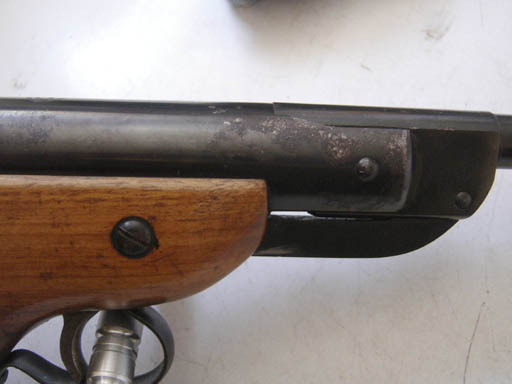
Well, if it were in perfect condition it would have been a steal, but there's a bunch of rust pitting on the right end of the action.
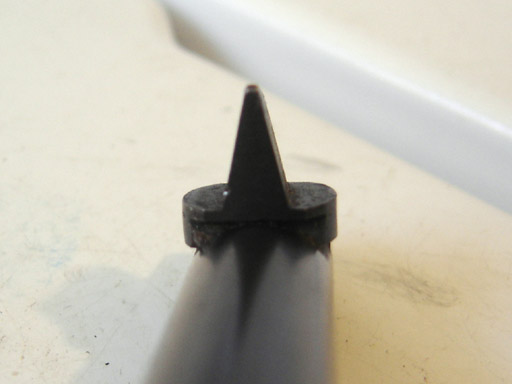
The triangular front sight.
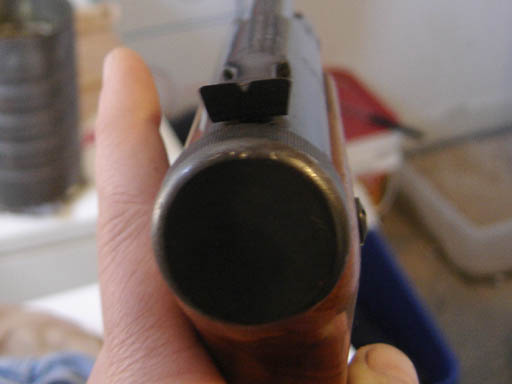
The vee rear sight.
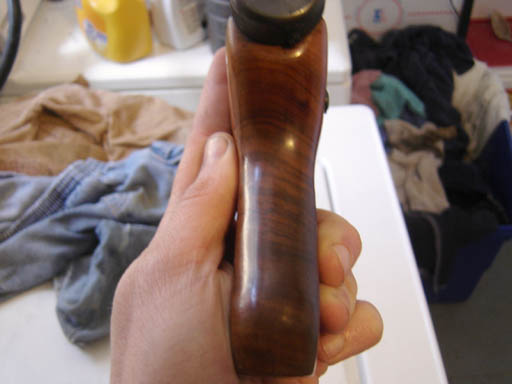
The wood grain is pleasing.
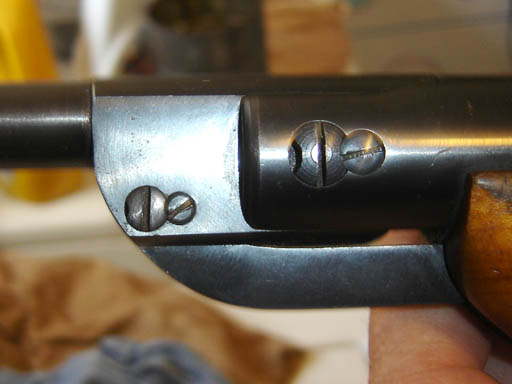
That's quality, not only is there a lock screw for the barrel pivot, but also for the link!
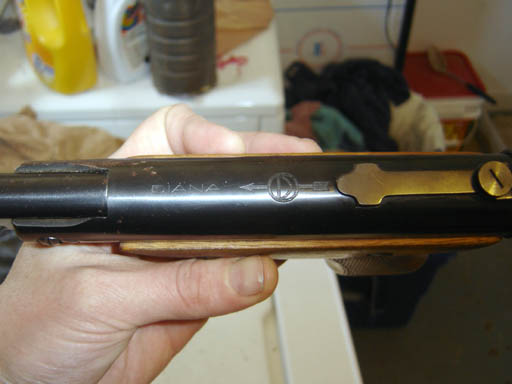
A slotted sight adjustment screw, and the logo across the top.
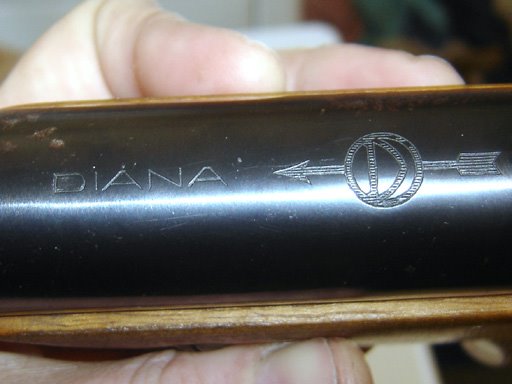
The D logo with an arrow running through it.
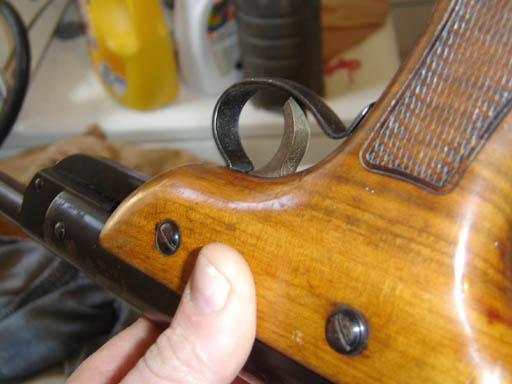
The trigger is solid, rather than a stamping.
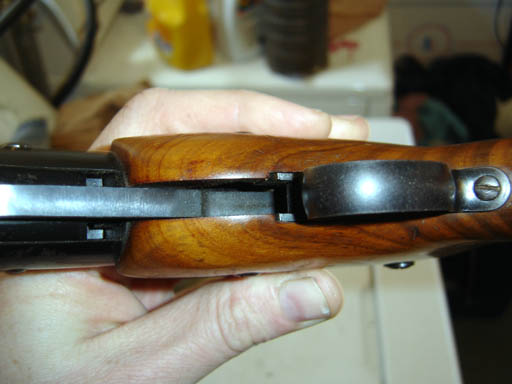
As is the linkage, solid steel.
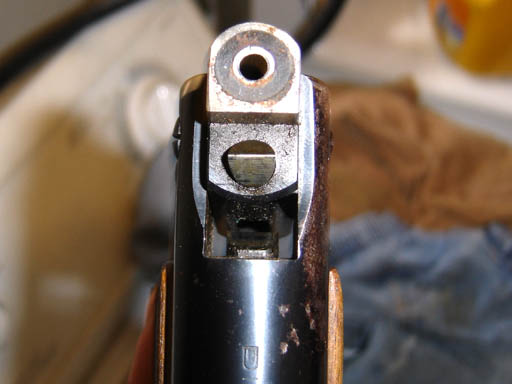
The breech washer is leather.
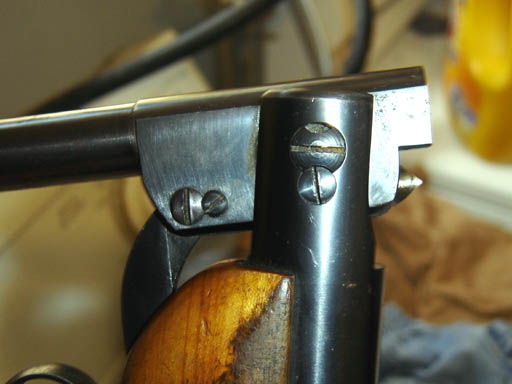
It has a vee detent. The pistol locks up solidly but is easy to break.
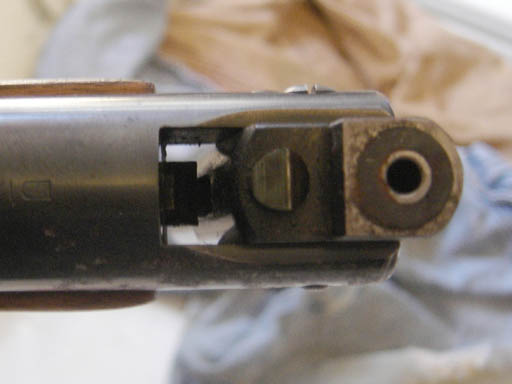
You can see the catch, rather than a machined pocket, down inside the slot.
Anyway, it seems to shoot well, at least as far as cans at 20 feet are concerned. I'll have to chrony it, oil the washer, and take some 10M shots to see how she (and I) group. I'm really delighted to have another beautiful vintage airgun, at a price I could afford, in my collection.