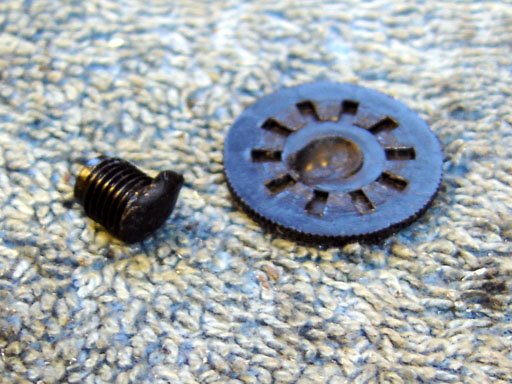
The two pieces.
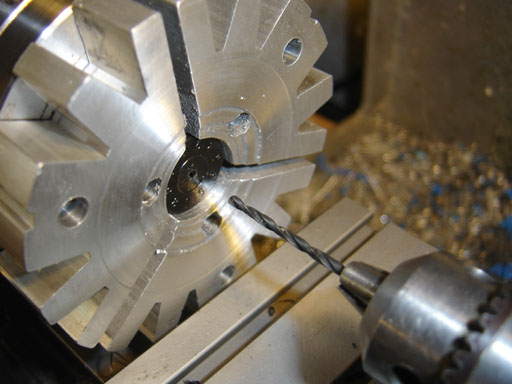
I drilled and countersunk the knob for a #2 flat head screw.
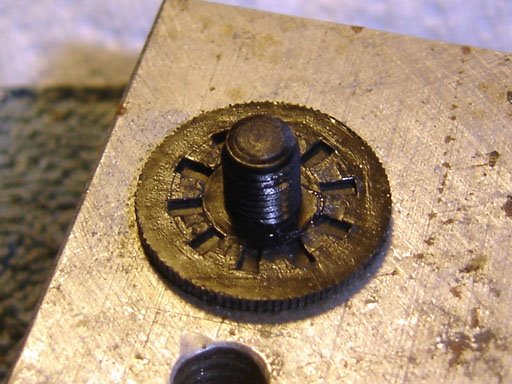
I superglued the two pieces together.

And then drilled and tapped the screw for a #2 thread.
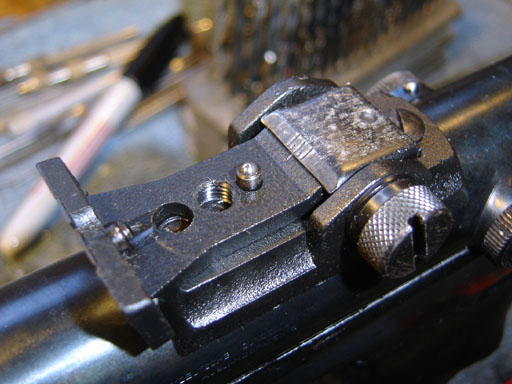
I reassembled the sight.
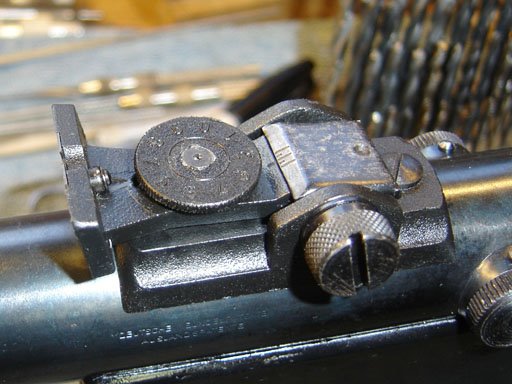
I schmeared a bit of JB weld into the hole and the countersink, and screwed a #2 flat head screw in, to hold it all together. When it was dry I screwed it into the sight assembly.
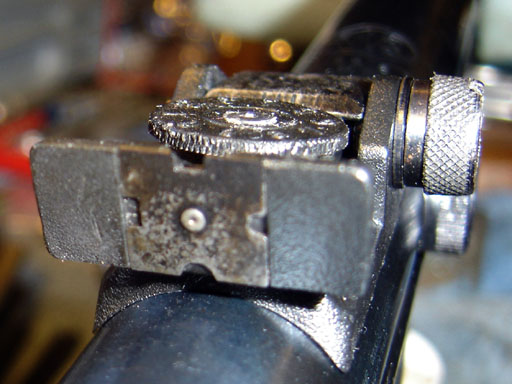
Up close it looked a bit rough, and wasn't good enough for what I wanted. Notice the neat 4 way rear sight notch.
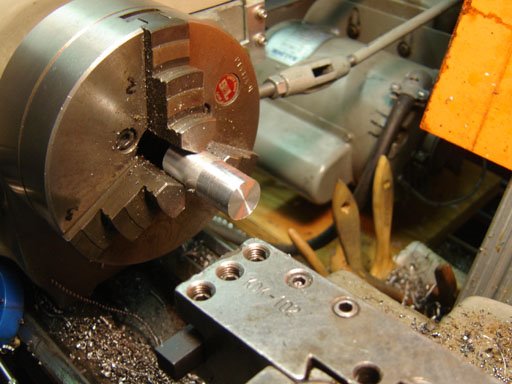
So I turned some aluminum stock to the knob OD.
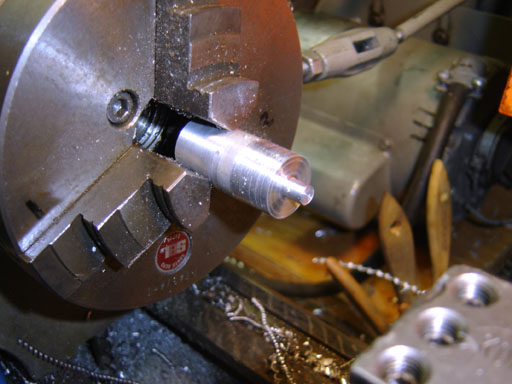
And turned down the end for the screw.
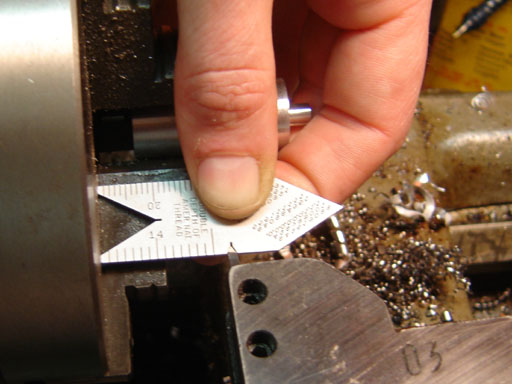
The screw diameter was about .222" and a left hand metric .75mm thread. The Jet 920 lathe does metric threading, but not left hand. The South Bend does left hand threads but not metric. To get either lathe to do both would take a lot of time and/or money (although I sense I'll have to do so in the future...) So I figured that a .75mm thread is 33.86 threads per inch. That's pretty close to 32 threads to the inch, .0017" of error per turn of the screw. For the short amount of thread engagement it should work fine.
I aligned the threading toolbit with a "fishtail" threading gage.
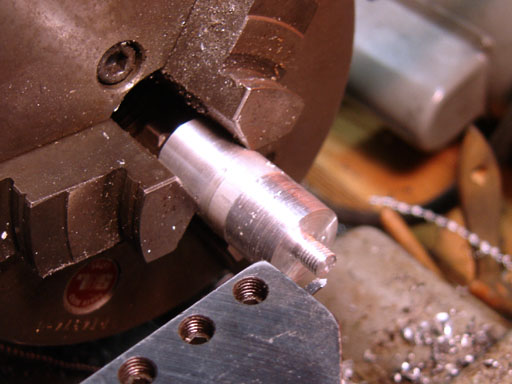
And turned the left hand 32 tpi thread in a few passes.
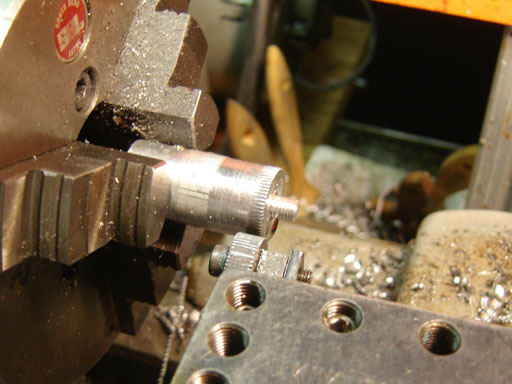
I loaded up my "made from scrap and a screw" straight knurling tool and knurled the edge.
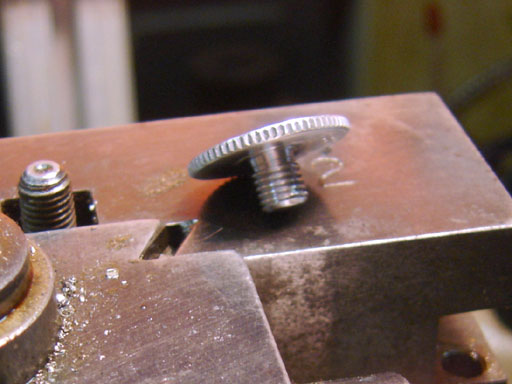
I used the parting tool to make a thread relief groove against the knob, so I could screw it all the way in, then parted off the knob.
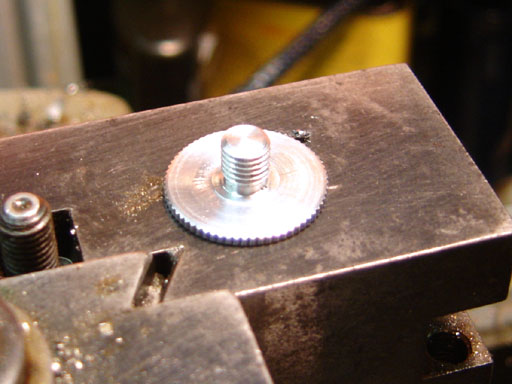
Not bad.

It screws in, a little tight but the sight body is plastic (sorry, it's "synthetic", which means "too cheap to make the damn part out of metal") and the screw thread will reform the to the screw.
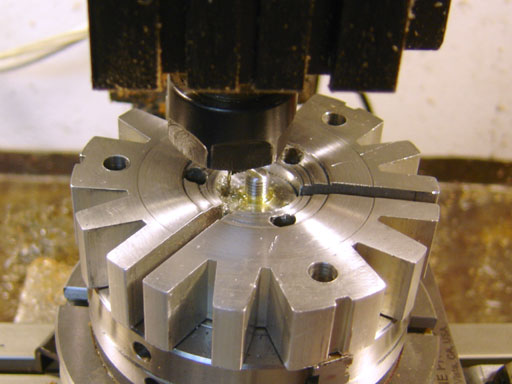
I then mounted the manual rotary table to the mill and used an end mill to make the detent notches in the underside.
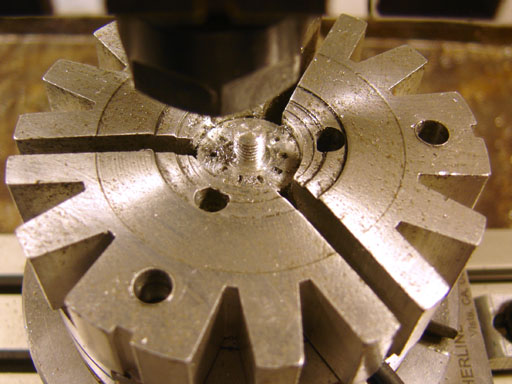
All done, if you squint, you can see that I messed up the spacing a bit on some of the detents, largely because it's the first time I used the Sherline manual rotary table with it's weird decimal angle knob. I also managed to get the depth wrong on one and milled all the way through.
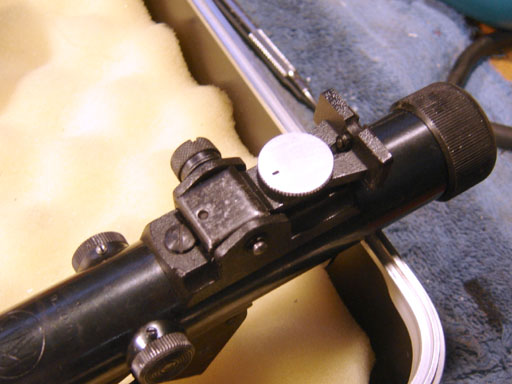
If I hadn't said I milled all the way through by accident you'd think I was a design genius, on par with Movado, to make such a modern looking and understated index mark. I don't see the utility of putting numbered index marks on the top of the knob, as you just get it zeroed in at 10M and forget it...
You've made my day! I am so glad you messed up, well not that you messed up but the fact that everybody messes up and that your man enough to tell us and not hide it tells volumes about your character.
ReplyDeleteI think I mess up at least (at least!) one part of each project I work on. It's how you handle the inevitable mistakes that really matters.
ReplyDeleteMy motto is that "The Perfect is the enemy of The Good Enough"
Pretty good repair on the sight. I have an old (5o +years) Colchester Student lathe and it serves me well.
ReplyDeleteI like the challenge of fixing broken things and it keeps my technical skills in tune.
I'm into airguns too and I've been tinkering for many years.
Nice blog and keep it up.
David.