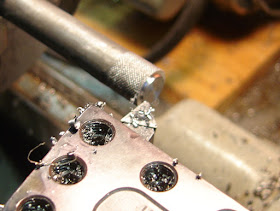
A smaller piece of steel, knurled and turned.
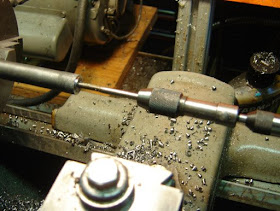
Tapping #8-32. The drawing calls out #8-36 but I'm a rebel. This does have implications down the line...
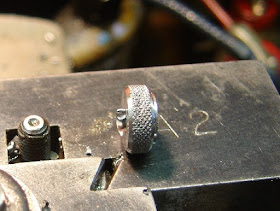
Parted off.
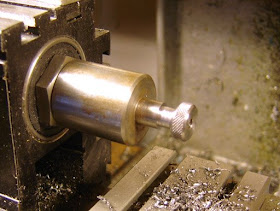
Mounted on a mandrel for facing off.

Done!
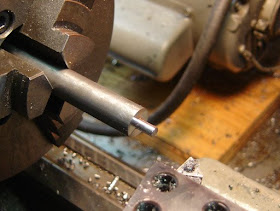
Now the aperture. Turned to diameter.
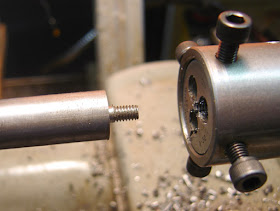
Threaded #8-32
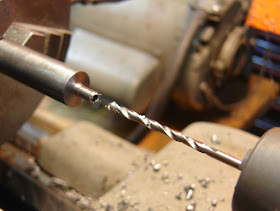
Drilling the major diameter. I reduced it a bit from the drawing to take into account the deeper thread depth of the #8-32 over the #8-36 (A difference of .003" thread depth)
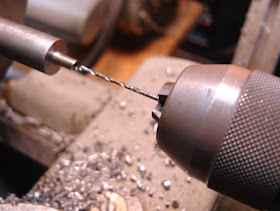
Drilling the aperture hole. I also reduced this, but mainly because I like a smaller aperture.
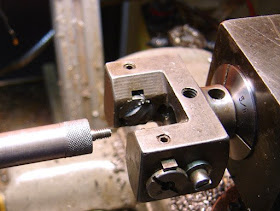
Knurling.
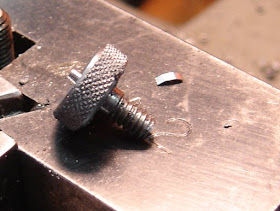
Parted off.
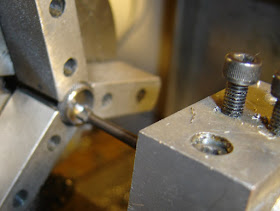
Blurry picture of boring out the face.
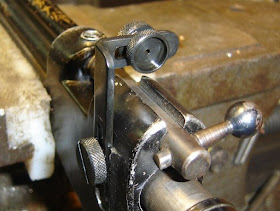
Blued with Oxpho blue and mounted on the rifle. Works fine. It's a fun and accurate rifle to shoot.