On I go.

The valve as removed from the 101. The screen at the end is not original, nor is the o-ring and metal washer?
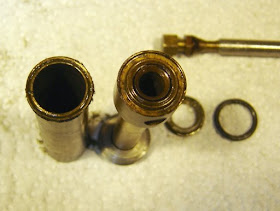
There should have been an asbestos gasket between these parts, but someone had evidently tried to reseal it and substituted the o-ring and possibly the washer.
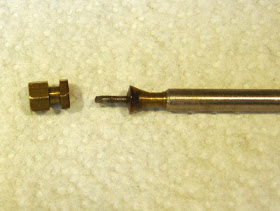
The P
yrasteel valve end unscrews. Not sure what the conical seal is made of.
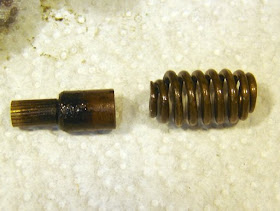
The inlet valve is crusty with disintegrated rubber.
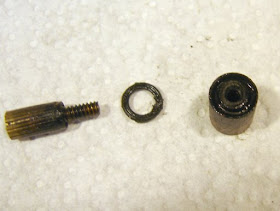
There was an o-ring there as well.
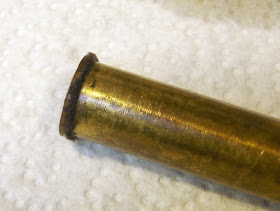
The remnants of the paper gasket (paper? fiber?).
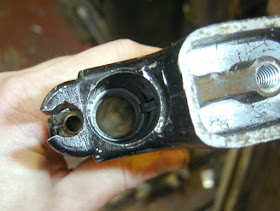
The tube is in good shape.
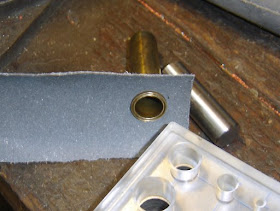
I fabricated a new gasket from gasket stock by punching a hole to fit the compression chamber.
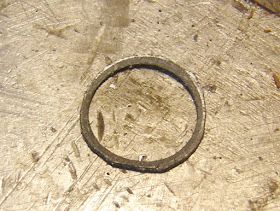
Then trimmed it with scissors.
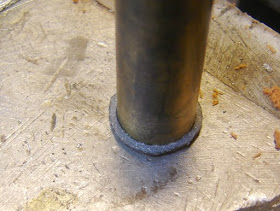
Not bad. If I wasn't keeping the system stock, this would be the time to cut an o-ring groove at the other end of the valve chamber, for better sealing with the tube. I'll do it on the next one. I'd either eliminate the gasket or make a thin one from
teflon or rubber.