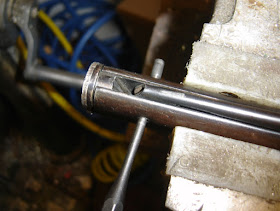
Punching out the pivot pin.
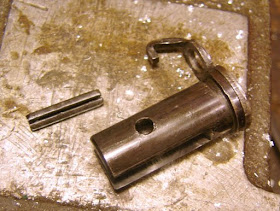
The pivot plug.
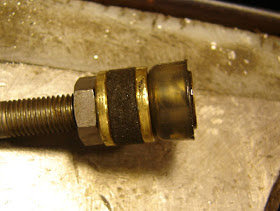
The pump cup (remember, it's a 101 pump head, and a replacement seal of unknown provenance). It didn't look bad but seemed floppy, not stiff.
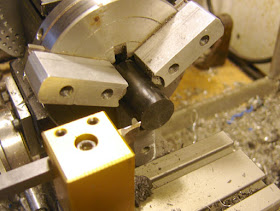
Some 95 durometer urethane rod being faced with my extreme knife tool. I ground a bunch of tools that have around 60 degrees rake, more or less.
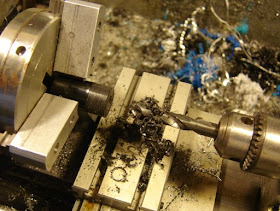
Drilling it out.
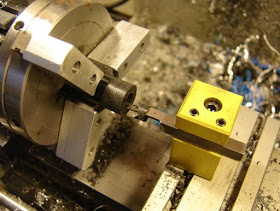
Boring the minor diameter.
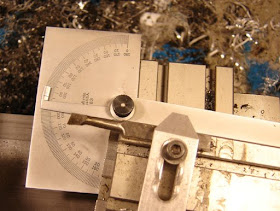
Setting the compound to about 5.5 degrees.

Turning the OD with a similar knife edge tool.
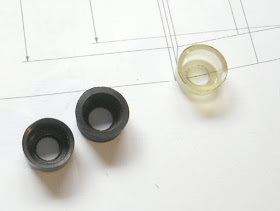
The new cup is the middle one. Left is the one that came with the 101.
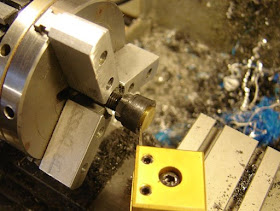
I assembled it but it seemed overly tight. I also forgot the bevelled edge on the face. So I disassembled again and mounted it on a broken pump rod. I cut the bevel and turned the OD slightly smaller.
I put it all back together and pumped it up 10 times. Air was leaking past the bolt. Shot again and the bolt shot under the cover (no pic, I was having an adrenaline rush) which was a bit dramatic.
So I refurbished the bolt cover with a hole on the other end and less clearance for the locking lug, and used the old screw from my 150 (it has a head so won't allow the bolt to sneak under the cover). Anyway, I just "won" an original bolt cover on Ebay, so when it comes I'll make a new screw and it should be close to perfect (?).
I pumped it up 10 times and got 636 fps, which is great. I think if I tighten up the bolt seal and maybe clean up the flow through bolt a bit it will gain a little more. Unless something else goes wrong...I am happy I was able to make a pump cup, which is a skill that should come in handy for other projects.