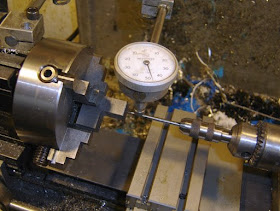
I chucked up a piece of L shaped steel in the 4 jaw chuck.
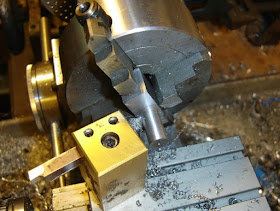
Turned a shaft on it.
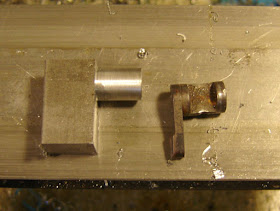
Looks like a safety already.
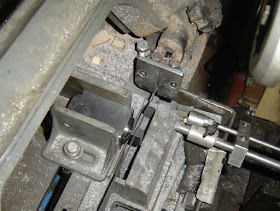
Sawed off the waste.
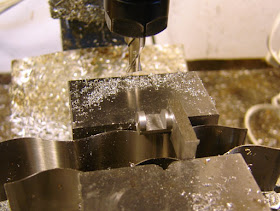
I put it backwards in the vise, alas, when cutting the notch for the safety plug.
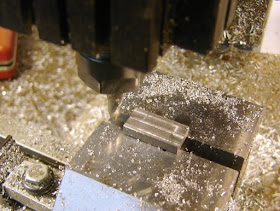
Milled it thinner.
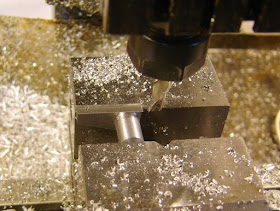
Trimming away.
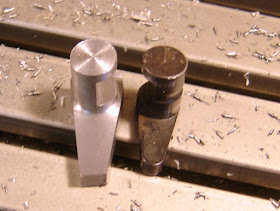
A rough, mirror image safety.
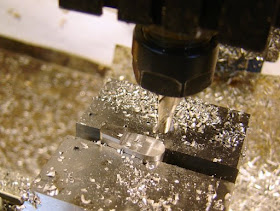
I rounded the corners on the belt sander, then milled away a bit more to make the lever.
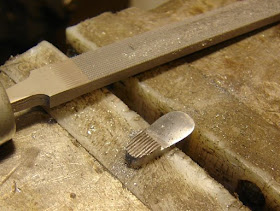
I used the checkering file to serrate the lever.
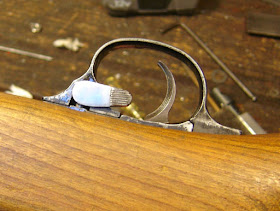
Well, it works, but it's the wrong way around.
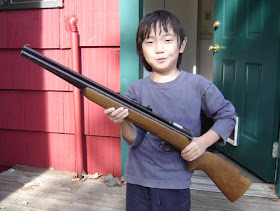
This is the guy who distracted me. But he makes a good gun rack.
There's still a bunch to do, assuming I can live with a backwards safety lever.
I drew up the bolt today, and hope to make it this weekend. Then I'll think about the final design for the breech cover.
I did run some rounds through the gun. Initial numbers were in the low 300's, at which point I realized I was loading .177 pellets in a .22 rifle. Distractions...anyway, it's shooting around 580 fps with 10 pumps (14.3 gr.), which is a little low. I hope that a new transfer port seal and a new bolt will speed it up a bit. We'll see.