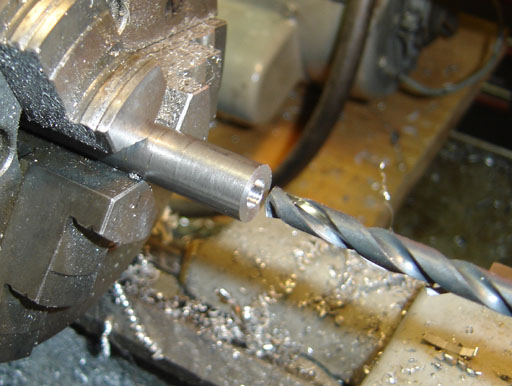
I need a knurled screw for the stock slider lock. Drilling for a press fit on a #8 SHCS.
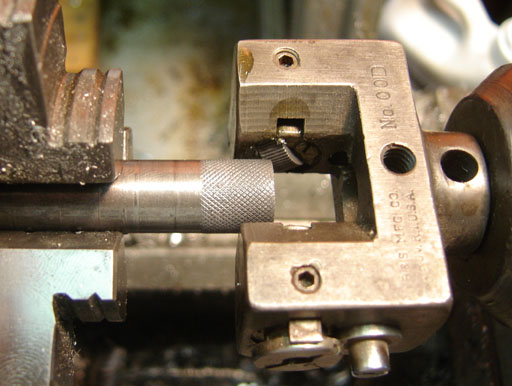
Knurling.
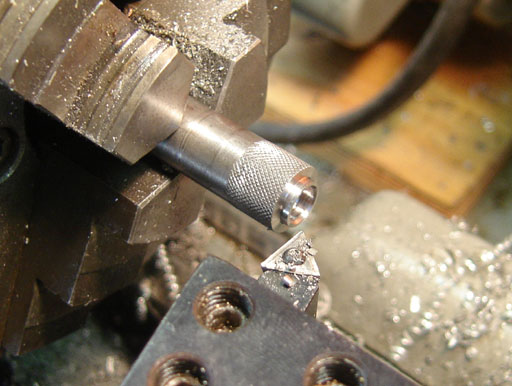
Cutting a shoulder.
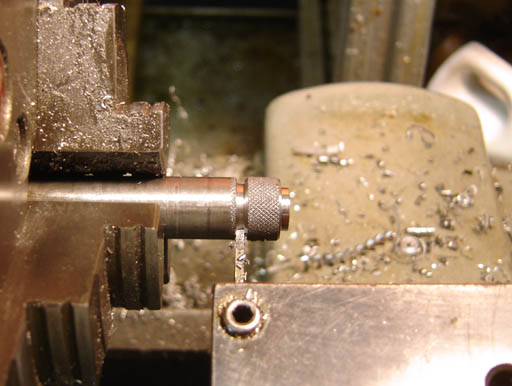
Parting off.
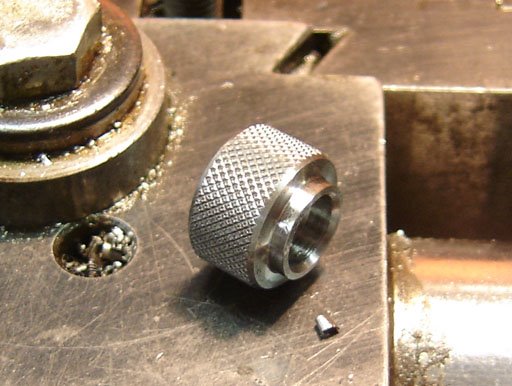
Ready to press onto a screw.
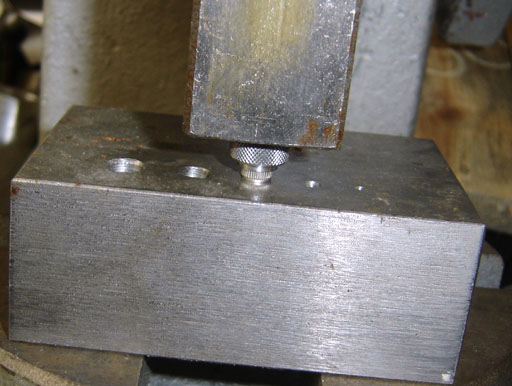
Pressing matters.
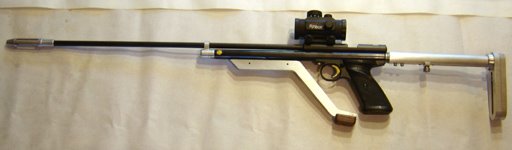
Here it is with the stock retracted.
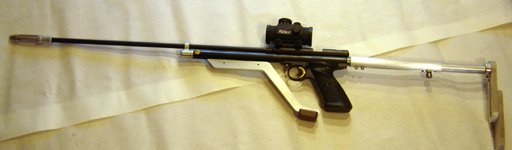
And the stock extended.
I need to learn how to take better pictures of rifles, when I get closer to being completely done I'll take some larger shots...
All that's left is maybe some new grips, some sort of sight although I may just keep the red dot sight, maybe a brass safety button, and some finishing on the aluminum bits. I don't know if I'll anodize, paint or just polish/finish the bare aluminum. We'll see. I also need to take some of the slop out of the pump linkage, it's a bit wiggly.
All that remains of the original 1377 is the grip frame, pump linkage, safety, sear, trigger, tube, grips (more or less, these came off of a 2300), hammer and hammer spring. This has certainly been a fun first modification project.